CLM 4.0 - Closed Loop Manufacturing 4.0
Der Digitale Zwilling bietet durch einen permanenten Datenaustausch zwischen der realen Werkzeugmaschine und deren virtueller Repräsentation sowohl Werkzeugmaschinenherstellern als auch Endanwendern zahlreiche Vorteile. Durch den Einsatz von physikalisch motivierten Simulationsmodellen und Ansätzen des maschinellen Lernens können dynamische Instabilitäten erkannt, das Schwingungsverhalten der Maschinenkomponenten identifiziert und Bearbeitungsprozesse während der Laufzeit optimiert werden.
Motivation und Zielsetzung
Der wirtschaftliche Einsatz von Werkzeugmaschinen ist maßgeblich vom Zeitspanvolumen sowie von Stillstandszeiten aufgrund von Rüst- und Wartungsmaßnahmen abhängig. Es ist somit der Wunsch von produzierenden Unternehmen, die Belegungszeit und die Anzahl notwendiger Instandhaltungsmaßnahmen zu reduzieren. Diese beiden Vorgaben stellen einen Zielkonflikt dar: Mit der Erhöhung von Vorschubgeschwindigkeiten und Schnitttiefen sinkt zwar die Hauptzeit, aber gleichzeitig ist ein Anstieg des Werkzeug- und Anlagenverschleißes die Folge. Das Ziel der Prozessregelung und -optimierung muss deshalb sein, dass trotz des Wunsches nach kurzen Zykluszeiten sowohl die Stabilitätsgrenzen der spanenden Bearbeitung eingehalten als auch die maximalen Maschinen- und Werkzeuglasten nicht überschritten werden.
Neben der sinkenden Werkzeug- und Anlagenstandzeit nimmt auch die Fertigungsgenauigkeit mit steigenden Vorschubgeschwindigkeiten und Schnitttiefen ab, da ansteigende Prozesskräfte höhere Formfehler verursachen. Des Weiteren kann der Regenerativeffekt durch Überschreiten der Grenzschnitttiefe zu Rattermarken auf der zu bearbeitenden Oberfläche führen.
Das Ziel des kanadisch-deutschen Forschungsprojektes Closed-Loop-Manufacturing 4.0 ist es durch den Einsatz einer virtuellen Abbildung des Bearbeitungsprozesses dynamische Instabilitäten zu vermeiden und die Vorschubgeschwindigkeit im Hinblick auf Maschinenbelastung und Formfehler zu optimieren. Um dieses Ziel zu erreichen ist es unerlässlich, das positions- und werkzeugabhängige Nachgiebigkeitsverhalten der Maschine zu bestimmen. Durch die Verwendung von indirekten Messgrößen und virtueller Sensorik kann die Frequenzantwort der Maschinenstruktur während der Bearbeitung gemessen werden. Eine experimentelle Modalanalyse mit einem Impulshammer oder einem Aktuator ist dadurch nicht notwendig. Außerdem ermöglicht die Online-Modalanalyse, das bestimmte Nachgiebigkeitsverhalten während des Lebenszyklus der Anlage stetig zu aktualisieren. Der Einfluss des aktuellen Verschleißzustands auf das dynamische Verhalten wird dadurch kontinuierlich abgebildet und in der Kompensation von Bearbeitungsfehlern berücksichtigt.
Vorgehen
Ein Edge-Computer greift über eine Netzwerkkommunikation auf die Maschinensteuerung zu und führt einen zweistufigen Regelkreis aus. Der innere Regelkreis führt die zeitkritischen Aufgaben der Rattererkennung und -vermeidung, der Kollisionsüberwachung und der Werkzeugverschleißdetektion aus. In der äußeren Regelschleife wird auf Grundlage des positions- und werkzeugabhängigen Nachgiebigkeitsverhaltens eine Optimierung der Bauteilprogramme durchgeführt. Dadurch soll sichergestellt werden, dass keine dynamischen Instabilitäten, nur geringe Konturfehler und kleine Bearbeitungskräfte während der Zerspanung auftreten. Aufgrund dessen bietet der Regelkreis neben einer gesteigerten Fertigungsgenauigkeit auch eine höhere Werkzeug- und Maschinenstandzeit. Die entscheidende Herausforderung dieses Forschungsvorhabens ist die Frage, wie eine möglichst hochfrequente Maschinendatenakquisition ohne umfangreiche Zusatz-Sensorik realisiert werden kann. Außerdem gilt es, die prozess-parallele Überwachung und Regelung des Bearbeitungsprozesses durch eine effiziente Identifikation und mathematische Beschreibung der Anlagendynamik zu ermöglichen.
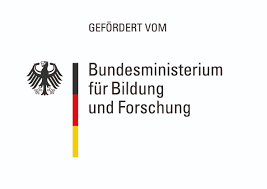
Laufzeit | 01.03.2019 - 28.02.2022 |
Förderer | Bundesministerium für Bildung und Forschung (BMBF) |