Abteilung Batterieproduktion
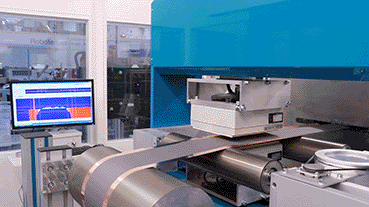
Leistungsfähige elektrochemische Energiespeicher sind für Anwendungen in der Elektromobilität und der stationären Energiespeicherung von großer Bedeutung. Hierfür sind die Verbesserung der gravimetrischen und volumetrischen Energiedichte sowie die Reduktion der Produktionskosten ausschlaggebend. Erst ein vertieftes Prozessverständnis über die Herstellung von Lithium-Ionen-Batterien (LIB) ermöglicht die Produktion verbesserter und kostengünstiger Batteriezellen.
Die Abteilung Batterieproduktion beschäftigt sich forschungsseitig deshalb mit der Fertigung von innovativen Batteriezellen. Der Kern der Arbeit ist die Prozessentwicklung und die Optimierung aller Prozesse innerhalb der Batterieproduktion. Vom Mischen der Elektrodenmaterialien bis hin zur Formierung der fertigen Zellen werden alle Schritte in-house an der Forschungsproduktionslinie des iwb durchgeführt. Die Arbeitssicherheit steht hierbei stets im Vordergrund. Auch aufgrund der industrienahen Forschung des iwb werden entlang der gesamten Prozesskette höchste Sicherheitsstandards eingehalten. Das Zellportfolio umfasst verschiedene Zelltypen (Knopf-, Pouch- und Hardcase-Zellen) mit Kapazitäten von wenigen mAh bis über 20 Ah. Hierfür steht am iwb industrienahe Anlagentechnik zur Verfügung, welche flexibel an verschiedenste Anforderungen angepasst werden kann.
Neben unterschiedlichsten Materialien konventioneller LIB beschäftigt sich die Abteilung auch mit Festkörperbatterien und der Verwendung von metallischem Lithium, sowie Silizium-Komposit-Anoden zur Herstellung von LIB der nächsten Generation.
Leitung der Abteilung: Sophie Grabmann
Forschungsschwerpunkte
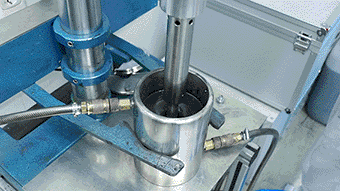
Elektrodendesign und -herstellung
Die Performance von Batteriezellen hängt nicht nur von den verwendeten Materialien, sondern auch maßgeblich von der Beschaffenheit der Elektroden ab. Jedes Elektrodenmaterial bedarf einer Neuauslegung der Herstellungsprozesse, weshalb ein vertieftes Verständnis über diese notwendig ist.
Im Forschungsfeld Elektrodendesign und -herstellung beschäftigen sich die Mitarbeiterinnen und Mitarbeiter intensiv mit neuen Elektrodendesigns (von Slurry-Rezepturen bis zu Elektrodenstrukturen) und der Verarbeitung neuartiger Elektrodenmaterialien. Kathodenseitig stehen vor allem kobaltarme Materialien auf NMC-, NCA-Basis sowie prälithiierte manganreiche Hochvoltspinelle im Fokus der Forschung. Für Anodenmaterialien liegt der Forschungsschwerpunkt auf Silizium-Kompositen und der Prälithiierung von Anoden.
Neben der Materialforschung und Forschung an Elektroden-Slurrys beschäftigt sich das iwb zudem mit der Auslegung von Elektroden- und Zelldesigns. Im Fokus stehen hier sowohl künstlich erzeugte Elektrodenstrukturen durch mechanische Strukturierungsverfahren und Laserstrukturierung, als auch natürlich erzeugte Strukturen durch den Einsatz unterschiedlicher Porositäten innerhalb der Elektrodenschichten.
Die innerhalb der Themengruppe Batterieproduktion betrachteten Prozesse reichen vom pulverförmigen Aktivmaterial bis zur fertigen Elektrode und umfassen das Mischen und Dispergieren, das Beschichten und Trocknen sowie das Kalandrieren und Laserstrukturieren der Elektroden.
Forschungsfeldleitung: Andreas Mayr
Zellproduktion und -qualität
In der Zellmontage werden aus einzelnen Elektroden funktionierende Zellen mit hoher Kapazität und Energiedichte produziert. Umso später Fehler entlang der Prozesskette auftreten, desto stärker wirkt sich der Ausschuss auf die Kosten aus, weswegen die Qualitätssicherung und Prozessstabilität höchste Wichtigkeit für eine effiziente Produktion unter hohen Materialkosten darstellt.
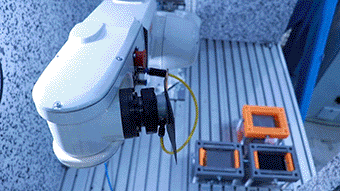
Das Forschungsfeld Zellproduktion und –qualität beschäftigt sich intensiv mit der Zellassemblierung und der Charakterisierung großformatiger Batteriezellen. Am iwb wird an den Prozessschritten Elektrodenschneiden (Laserschneiden und Stanzen), automatisierter Stapelbildung, Kontaktierung, Elektrolytbefüllung und Formierung geforscht. Die verschiedenen Einflüsse der einzelnen Prozessparameter auf die fertige Batteriezelle werden genauestens untersucht und die Parameter speziell auf die verwendeten Materialien und die Anforderungen an die Zelle angepasst. Um entlang der Prozesskette eine hohe Produktivität, eine gute Qualität und geringe Kosten gewährleisten zu können, setzt das iwb auf innovative Qualitätssicherungsmethoden und eine datenbasierte Prozessüberwachung. Innerhalb der einzelnen Prozesse sorgen verschiedene inline Qualitätssicherungsmaßnahmen für das Einhalten der geforderten Spezifikationen. Nach jedem Prozessschritt durchläuft das Zwischenprodukt zudem verschiedene Qualitätskontrollen, bevor es an den nächsten Verarbeitungsprozess übergeben wird. Hierdurch wird eine gleichbleibende, sehr hohe Qualität der produzierten Zellen gewährleistet.
Forschungsfeldleitung: Alessandro Sommer
Ausstattung im Bereich Batterieproduktion
- Beschichtungsanlage: Coatema BC 50
- Beschichtung von Batterieelektroden auf Technikumsmaßstab
- Variables Auftragswerkzeug: Schlitzdüse und Rakel
- Infrarot- & Inertgastrocknung mit drei separat ansteuerbaren Trocknungssegmenten
- Qualitätsüberwachung: Lichtwellensensor zur Dickenbestimmung und Ultraschallmessung zur Bestimmung der Flächenbeladung
- E-Cutter: Anlage zum Schneiden von Elektrodenblättern
- Konturschnitt für kontinuierlich und intermittierend beschichtete Elektroden
- Gepulstes Lasersystem für materialschonenden Schneidprozess
- Formatflexibilität durch 3-Achs-Laserscanner
- Unterdruckspannvorrichtung und Partikelabsaugung
- Automatisierte Materialzuführung mit Bahnkantensteuerung
- Elektrolytbefüllanlagen
- Vakuum- und Schutzgasatmosphäre zur Reduzierung des Wassergehalts während der Elektrolytbefüllung
- Formatflexible Zellhalter für großformatige Pouch- und Hardcasezellen
- Präzise Dosierung der Elektrolytmenge mit gravimetrischen Qualitätschecks
- Zusätzliche mobile Befüllanlage mit Überdruck- und Temperiermöglichkeiten für gezielte Prozessuntersuchungen
- Glovebox „Labmaster Pro SP“ mit 4 Handschuhe
- Arbeiten unter kontrollierter Atmosphäre mit <1ppm Sauerstoff und Feuchte
- Modular erweiterbares Glovebox-System MB-MOD mit 2 Arbeitsplätzen
- Regelbarer Vakuumofen bis 250°C mit Parameterüberwachung und Temperaturkontrolleinheit
- Reinraum ISO-Klasse 6 (100 m²) für die Elektrodenherstellung
- Beschichtungsanlage (Bahnbreite bis 300 mm) mit Infrarot-Trocknung und Inline-Flächenbeladungsmessung
- Rasterelektronenmikroskopie (REM): JEOL JSM-IT200 InTouchScope
- Voll ausgestattetes Raster- elektronenmikroskop mit Wolframkathode und integrierter EDS-Analyse
- Höchste Bildauflösung im HV/LV/SE/BSE-Modus
- Zeromag-Modus für Übergang zwischen lichtoptischen und REM-Bild
- Chemische Analytik durch integriertes EDS mit Live-Analyse
- Mehrkanal-Live-Bild und Videoaufnahme gleichzeitig möglich
- Smile View Premium Offline-Software mit Bildschärfung, Bildmontage, Positionsausrichtung und Überlagerung
-
Anlage zum Ultraschallschweißen: Kontaktierung von Elektrodenstapeln
- Fügen der unbeschichteten Elektrodenfähnchen
- Anschweißen von Ableiter-Tabs
- Kontaktieren von einlagigen sowie von mehrlagigen Pouch- oder Hard-Case-Zellen
- definierte Länge der Elektrodenfähnchen durch integrierte Schneideinrichtung
- Partikelabsaugung
- Halbautomatisierte Materialzuführung mit Werkstückträgersystem
- Z-Falter der Manz AG
- Automatisierte Z-Falter-Anlage zur kontinuierlichen Stapelung großformatiger Elektroden
- Formflexible Werkzeugeinsätze für das Stapeln unterschiedlicher Elektrodenformate
- Möglicher Einsatz verschiedener Separatormaterialien und -breiten
- Optische Überwachung der Positioniergenauigkeit
- Regelung der Separatorposition für eine zielgenaue Stapelung der Elektroden
- Vakuum-Umluft-Trockenschrank Typ HCV der Firma Waldner Process Systems
- Trocknung großformatiger Elektroden und Coils unter Vakuum
- Variabel einstellbare Trocknungzeiten, -temperaturen und Vakuumstufen
- Abfahren von Trocknungsprofilen für eine gleichmäßige Trocknung der Elektroden
- Zwei Trockenräume (100 m²) für die Zellmontage
Für die Untersuchung von Lithium-Ionen-Zellen stehen eine Vielzahl an Zelltestsystemen zur Verfügung.
- BaSyTec CTS
- BaSyTec CTS LAB
- BaSyTex XCTS
- Biologic BCS-815
- Biologic VSP-3e
- Gamry Interface 5000E
Temperierkammern für die Prüfung:
- Vötsch VT 4021-S mit Sicherheitsausstattung (-40 – 180 °C)
- Vötsch LabEvent T/210/40/3 mit Sicherheitsausstattung (-40 – 180 °C)
- Vötsch TempEvent T/340/40/3 mit Sicherheitsausstattung (-40 – 180 °C)
- Espec SU-242 (-40 – 150 °C)
- Binder ED-115 (20 – 300 °C)