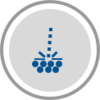
Innovative Process Strategies in PBF-LB/M
Nowadays, the exposure in laser-based powder bed fusion of metals (PBF-LB/M) is conducted vector-based with Gaussian intensity distribution and spot sizes in the range of 40 µm - 120 µm. In the research field “Innovative Process Strategies in PBF-LB/M“ state-of-the-art exposure is extended by strategies with spatial and temporally shaped laser radiation.
Aim
The investigations in the research field “Innovative Process Strategies in PBF-LB/M” pursue different goals with regard to the process itself and the resulting component properties:
- Increased process reproducibility by reduced process dynamics
- Increased process productivity or rather process speed
- Support-free build process and high surface qualities as well as geometrical accuracy
- Tailored component properties
Reaching these often contradictory goals with state-of-the-art exposure strategies is challenging. New innovative exposure strategies are needed. Investigating the influence of these novel strategies on the PBF-LB/M process and the resulting component properties is essential for the industrialization and establishment of additive manufacturing as a robust and economical manufacturing process.
Methodology
To achieve the goals mentioned above and to extend and tailor the PBF-LB/M as desired, both temporally and spatially shaped laser radiation in the PBF-LB/M process is investigated by the following methods:
- pulsed exposure strategies
- alternative beam profiles with variable spot sizes
Both types of process adaptation also influence the cooling and solidification conditions and thus the formation and expression of the resulting microstructure and component properties.
Vision
By the consistent analysis of temporally and spatially shaped laser radiation, the fundamental process insight of the PBF-LB/M is enhanced and process-structure-property relations for new exposure concepts can be deduced. In this way, it will be possible in the long term to adapt the process and the resulting component properties to different target values. Thus, the process and the properties of the additively manufactured components can then be tailored voxel by voxel.