FOREL2 – Centre for Research and Technology for Resource-efficient Lightweight Structures of Electromobility 2
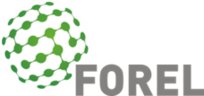
Motivation
Political and societal requirements for the future of mobility – sustainability, user-friendliness, and efficiency – are the focus of numerus research activities. The centre for research and technology for resource-efficient lightweight structures of electromobility (FOREL), as a national and open platform, not only addresses innovative joining technologies and process chains, but also serves as a sustainable bridge between industry and research. After three successful years, the establishment phase of the joint project has started. FOREL2 will revolve around linked process chains as well as the initiation and systematic coordination of research projects, such as PROLEI. To extend the range of subjects, the consortium of the initiation phase, consisting of the Institute of Lightweight Engineering and Polymer Technology (ILK, Technical University of Dresden), the Laboratory for Materials Engineering and Joining Technology (LWF®, Paderborn University), the Institute of Mineral Processing Machines (IAM, Freiberg University of Mining and Technology) and the Institute for Machine Tools and Industrial Engineering (iwb, Technical University of Munich), is complemented by the Institute of Forming Technology and Lightweight Construction (IUL, Technical University of Dortmund).
Objective
The objective of FOREL2 is to systematically expand on and enhance the progress made in the initiation phase, and to support Germany as a leading supplier and market for electromobility. The primary emphases lie on innovative and established technologies used in structural lightweight design and process chains for sustainable production. The evaluation of the maturity level of the technologies and the process chains are of particular relevance for FOREL2.
Approach
In order to assess the implementation potential of innovative lightweight design strategies, various thermal joining technologies used in technical production areas will be systematically classified in technology profiles. The profiles will then be used as a guide for assessing both established and novel joining technologies for use in resource efficient and lightweight design. These will be methodically rated, for instance based on their compatibility with various material combinations for lightweight design. Additionally, the characterisation of joints manufactured through a given joining technology plays an important role in determining the technology’s potential and degree of maturity. Increasing in the workpiece flexibility and reducing the number of different joining technologies employed are core issues when it comes to designing resource-efficient lightweight structures. Hence, the technology profiles will be employed to assess the potential of innovative thermal joining technologies for use in lightweight applications and to illustrate the stages of technological evo-lution. Above all, insight into both the generic modification of existing systems and the development of new techniques will be provided. Through this process, the influence of new concepts on established joining processes will be clearly ex-plained. Lastly, the acquired results will be merged and used to derive practical „Greenfield joining-concepts“ for car body construction. The second area of emphasis in this project is focused on the “technology evaluation”. The objective of this work package is to develop a software-tool that determines the maturity level of a technology for use in electromobility applications. The first step in this process to establish requirements based the interdisciplinary topics addressed in FOREL2, namely: joining, forming, recycling, and/or dismantling technologies. Selecting the proper software lays the groundwork for the implementation as well as for the product and product-related expansion of the methodical evaluation of technologies. The extension of the evaluation technologies arises from the requirements of the production environment for electromobility. The evaluation of the constructed method (i.e. software-tool), is conducted by project partners within FOREL-related technology projects and builds an iterative loop for further improvements. Finally, in order to test the software, an exemplary evaluation of process chains is implemented within the context of the car body production at an automobile manufacturer
Acknowledgement
This research and development project is funded by the German Federal Ministry of Education and Research (BMBF) within the Framework Concept “Research for Tomorrow’s Production” (funding number 02P16Z010–02P16Z014) and managed by the Project Management Agency Karlsruhe (PTKA). The author is responsible for the contents of this publication.
Homepage
Duration | 01.12.2016 – 30.11.2019 |
Partners | Institute of Lightweight Engineering and Polymer Technology (ILK, Technical University of Dresden) |
Laboratory for Materials Engineering and Joining Technology (LWF®, Paderborn University) | |
Institute of Mineral Processing Machines (IAM, Freiberg University of Mining and Technology) | |
Institute of Forming Technology and Lightweight Construction (IUL, Technical University of Dortmund) | |
Funded by | German Federal Ministry of Education and Research (BMBF) |
Project Management Agency Karlsruhe (PTKA) |