Koresil - Concepts for the resource-efficient and safe production of lightweight structures
Motivation
The function-integrated lightweight construction in multi-material design in the area of tension between economy, ecology and social aspects requires the linking of various engineering disciplines. The rapidly advancing digitalization and the increasing importance of virtual processes are additionally changing the future world of work. Particular challenges are the mastery of innovative and closed process chains in the processing of different materials and the production of highly integrative lightweight structures.
Goal
The prime objective of KORESIL is the combination of production technologies, as well as their virtual illustrations, which up to date have been considered isolated for an application in the field of lightweight construction. On the one hand, the increasing complexity that humans are confronted with in the production environment is to be reduced and made controllable by means of novel tools. On the other hand, the feasibility of resource-neutral production is to be demonstrated using the example of a closed process chain.
Consortium
The project consortium includes the Institute for Machine Tools and Industrial Management (iwb) at the Technical University of Munich, the Institute for Lightweight Engineering and Polymer Technology (ILK) at the Technical University of Dresden, the Laboratory for Material and Joining Technology (LWF) at the University of Paderborn, the Institute for Forming Technology and Lightweight Construction (IUL) at the Technical University of Dortmund and the Institute for Processing Machines at the Technical University of Bergakademie Freiberg.
Work content
As a basis for addressing the issues of technology development, process chains and the interaction between humans and technology, five test plants are to be set up which will be linked to form a closed process chain with a closed material and information loop. Starting with aluminum recyclate, a modified extrusion process (IUL) will be implemented. The profiles produced are then functionalized in the laser cladding (iwb) and partial plastic injection molding (ILK) processes. Different methods for joining and disjoining are investigated (LWF). The process chain and the material cycle are closed through a material cycle management (IAM). On the basis of the real experimental plants, primary socio-technical issues concerning workplace design and process optimization are investigated.
Utilization of results
The results are included into the national open platform FOREL. In this platform, technological gaps are identified and new funding projects are initiated. The success factor of the FOREL platform is the experimental development of technologies and methods that go far beyond the state of the art. The aim is to develop technologies for the entire product life cycle in the factory of the future and at the same time to demonstrate their potential for a safe and attractive workplace design. This includes, for example, online life cycle assessment, augmented reality and collaborative robots.
Acknowledgment
The research and development project KORESIL is funded by the German Federal Ministry of Education and Research (BMBF) in the program "Innovations for tomorrow's production, services and work" (funding codes 02P20Z000 – 02P20Z004) and managed by the Projektträger Karlsruhe (PTKA).
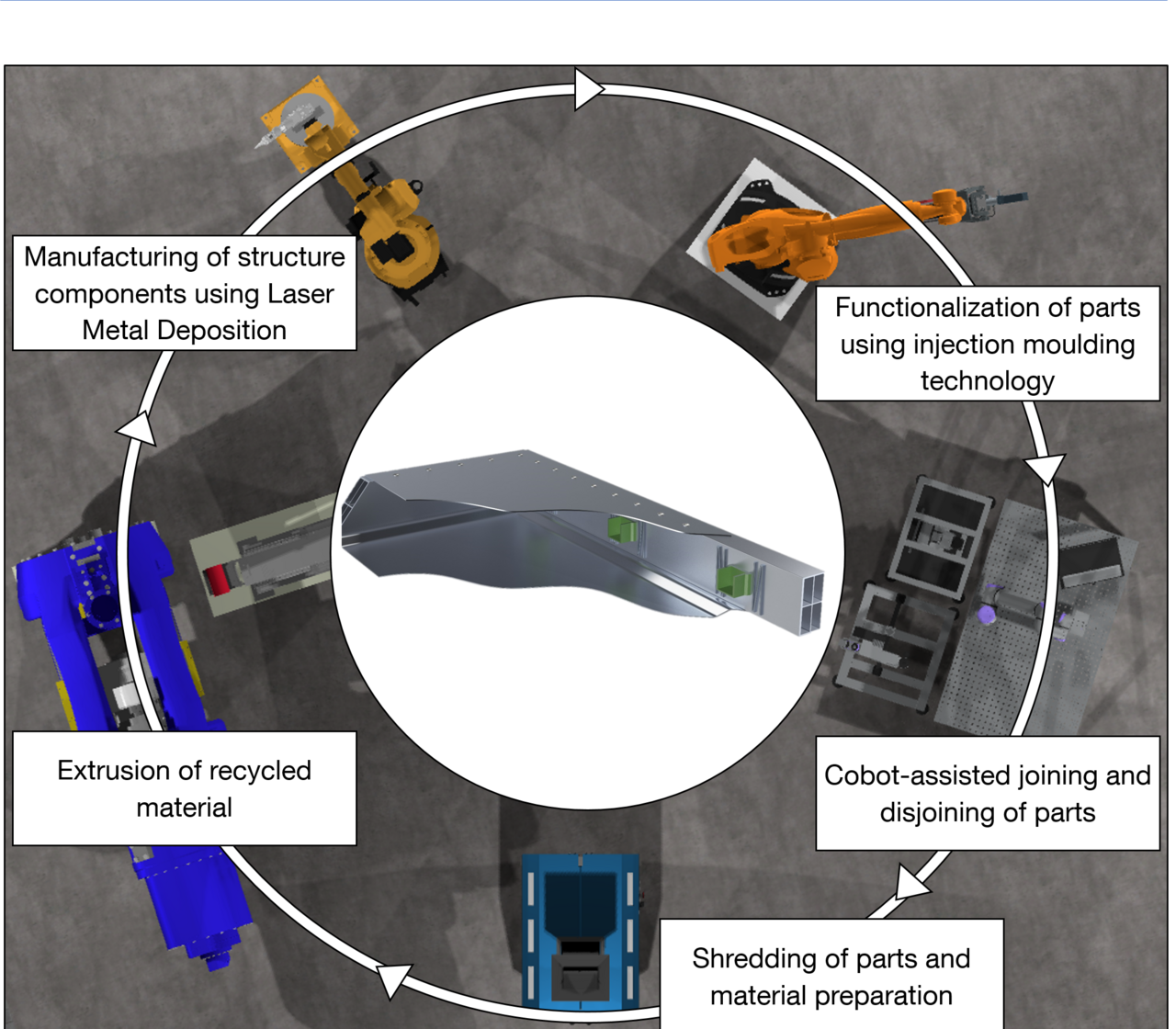