ProKIRo - Probabilistic methods of Artificial Intelligence in robot modeling for use in manufacturing technology
Due to their extraordinary flexibility in industrial manufacturing processes, the use of milling robots promises a significant increase in efficiency compared to conventional machine tools. Especially when machining large-volume components, their advantages, such as low acquisition costs combined with a large work space, come into effect.
However, their use is often limited by the low static and dynamic stiffness of the robot: due to the acting process forces, the Tool Center Point (TCP) of the robot is strongly displaced from the planned path during the process. Unless this displacement can be minimized by upstream compensation control or in-process process control, this will lead to unacceptable shape deviation from the nominal geometry of the part.
Preliminary work in this area has shown that modeling these robot properties is possible either by physically motivated robot models or by data-driven machine learning algorithms.
Together with the toolcraft AG, located in Georgensgmünd, Germany, the iwb addresses the fusion of both information sources using modern machine learning algorithms and aim at increasing the accuracy of milling robots in metal-cutting processes.
In order to continuously monitor the position-dependent static compliance of the robot in the process, the displacements of the TCP due to external forces and torques must be measured. A modern robot system from the swiss robot manufacturer MABI Robotic is used to record the displacements. The process-induced forces and torques can be recorded during the process by a sensory tool holder from pro micron GmbH.
We would like to thank the Bavarian Ministry of Economic Affairs, Regional Development and Energy (StMWi) for funding the ProKIRo project (Probabilistic artificial intelligence methods for robot modeling for use in manufacturing technology).
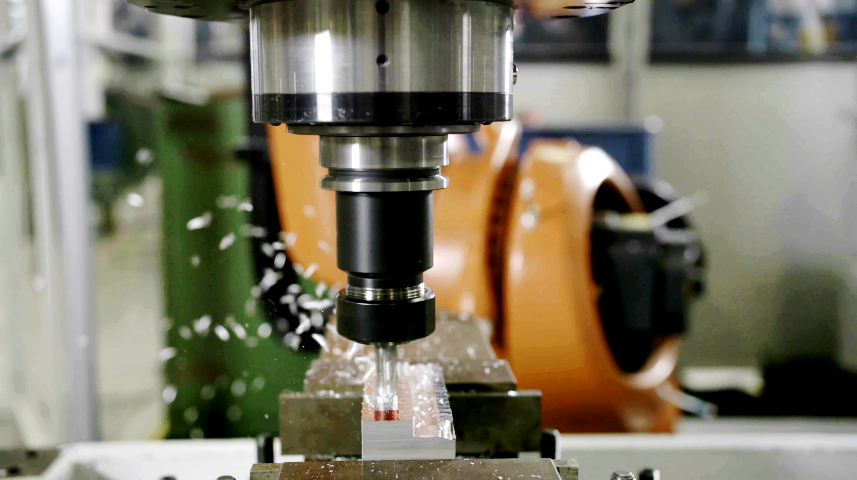