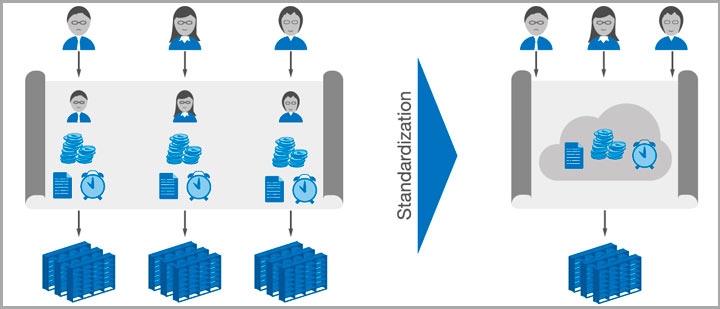
Identifizierung von Standardlösungen in der Lagersystemplanung
Aufgrund der Vielzahl an technischen Lösungsmöglichkeiten, kurzen Produktzyklen und einer unsicheren Marktlage geht einer hohen und langfristigen Investition in ein Intralogistiksystem meist ein aufwendiges, kostenintensives und langes Planungsprojekt voraus. Dieses wird häufig von Experten, Generalunternehmern oder den Systemherstellern selbst durchgeführt, da insbesondere kleine und mittelständische Unternehmen (KMU) oft keine personellen wie fachlichen Kapazitäten zur Projektabwicklung besitzen. Ergebnis dieser Planungsprojekte ist ein maßgeschneidertes Intralogistiksystem, welches die Anforderungen des Kunden optimal erfüllt.
Die kundenspezifische Entwicklung führt unter anderem bei der Planung des Teilsystems Lager dazu, dass trotz vergleichbarer Anforderungen, Projektziele und Ergebnisse dieselben Planungsschritte mit sehr ähnlichen Ergebnissen in mehreren Projekte parallel und unabhängig voneinander ablaufen. Auf diese Weise entstehen in jedem dieser Projekte Kosten, die durch eine Standardisierung deutlich verringert werden können. Diese vermeidbaren Kosten betreffen insbesondere KMU, da hier aufgrund geringerer Investitionsvolumina großer Bedarf an wirtschaftlichen Standardlösungen besteht und Fehlinvestitionen besonders kritische Auswirkungen haben. Um diese Planungsprozesse zu vereinfachen, zu verkürzen und besser abzusichern, wird in diesem Forschungsprojekt zunächst ein Vorgehensmodell zur Identifizierung technisch und wirtschaftlich standardisierbarer Planungsprozesse und -ergebnisse entwickelt. Diese identifizierten Standardlösungen zeichnen sich dadurch aus, dass sie die Kundenanforderungen möglicherweise nicht optimal, aber angemessen abbilden. Anschließend wird ein standardisierter Planungsprozess zur effizienten Realisierung der identifizierten Standardlösungen entwickelt. Durch die Standardisierung wird zudem die Fehleranfälligkeit des Planungsprozesses gesenkt sowie die Planungssicherheit erhöht. Angesichts der deutlich geringeren Investitionskosten, der deutlich geringeren Projektlaufzeit und der geringeren Planungsunsicherheit ist eine solche Standardlösung eine wirtschaftliche Alternative zur kundenspezifischen Individuallösung.
Um die Zielsetzung zu erreichen, wird das Projekt in mehrere Arbeitspakete (AP) untergliedert. Zunächst wird in AP 1 mithilfe einer Literaturrecherche eine theoretische Basis für die weitere Bearbeitung des Forschungsprojekts geschaffen. Darauf aufbauend wird in AP 2 der Lösungsraum der Standardlösungen identifiziert. Dieser wird in AP 3 über veränderliche und festgelegte Planungsparameter definiert. Zu den betrachteten Parametern zählen unter anderem die Lagermaße oder die verwendeten Ladehilfsmittel. Anschließend werden in AP 4 die Subsysteme definiert, aus denen die Standardlösung zusammengestellt wird. In AP 5 wird das Planungsvorgehen für ausgewählte Projekte bei einem Industriepartner dokumentiert und analysiert. Mithilfe dieser Daten erfolgt der Entwurf eines Planungsprozesses, in dem die Standardlösung geplant wird. Die Ergebnisse der Arbeitspakete 3, 4 und 5 werden in Arbeitspaket 6 in einen Software-Demonstrator implementiert. Dieser führt den Benutzer durch den Planungsprozess und erzeugt zu der passenden Standardlösung die notwendige Dokumentation. In AP 7 werden alle vorangehenden Ergebnisse zu einem Vorgehensmodell zur Identifizierung und Planung von Standardlösungen in der Lagersystemplanung zusammengefasst. Während der gesamten Projektlaufzeit erfolgt in AP 8 die wissenschaftliche Dokumentation und Publikation der Forschungsergebnisse.
- Jungheinrich Logistiksysteme GmbH
Das Forschungsprojekt wird im Rahmen eines Promotionsstipendiums der Dr. Friedrich Jungheinrich-Stiftung durchgeführt.