AdDEDValue – Vollautomatisierte Additive Fertigung mit DED-Verfahren für die automobile Serienproduktion
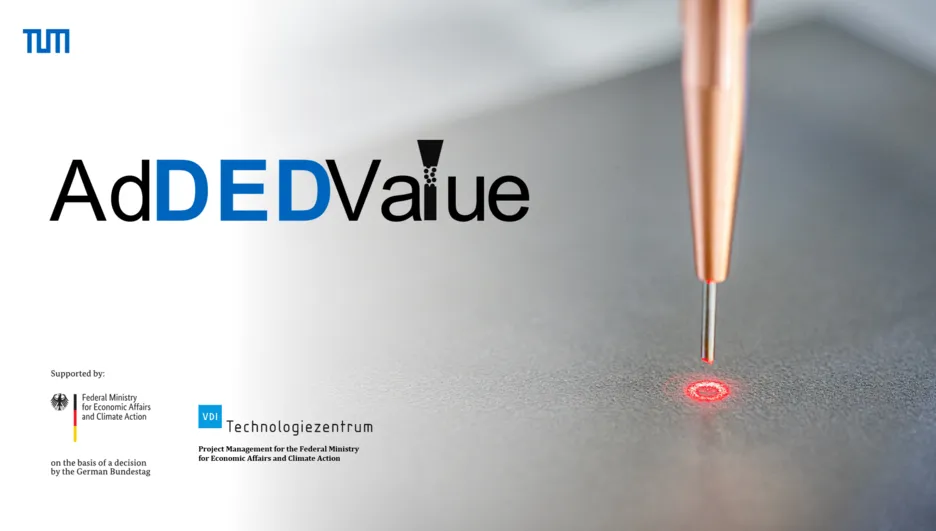
Projektüberblick
Im Projekt AdDEDValue wird ein Innovationssprung in der Produktion der deutschen Fahrzeug- und (Fahrzeug-)Zulieferindustrie angestrebt. Als zentrale Technologie wird dafür die metallbasierte Additive Fertigung eingesetzt, wobei Bauteile durch ein wiederholtes Auftragen von Schichten aus einem draht- oder pulverförmigen Ausgangsmaterial hergestellt werden. Im Speziellen kommen mit dem Laserauftragschweißen (LMD) und dem Wire Arc Additive Manufacturing (WAAM) sogenannte DED-Verfahren (DED: Directed Energy Deposition) zum Einsatz. Diese Verfahren stellen aufgrund ihrer hohen erzielbaren Auftragsraten nicht nur in der Einzelteilfertigung, sondern auch in der Mittel- und Großserienproduktion eine wirtschaftliche Alternative zu etablierten Fertigungsverfahren dar. Der Fokus des Projekts liegt auf der wertschöpfenden Nutzung von Prozess-, Anlagen- und Bauteildaten über die gesamte Fertigungskette hinweg, was durch den fortschreitenden Digitalisierungsgrad in der Automobilproduktion ermöglicht wird. Dadurch sollen die in AdDEDValue demonstrierten Produktionssysteme eine automatisierte Prozessauslegung, eine Echtzeit-Prozessregelung sowie eine zuverlässige und nachvollziehbare Qualitätssicherung erlauben. Eine angepasste Nachbearbeitung der produzierten Bauteile sowie eine fundierte Bewertung der untersuchten Technologien runden den ganzheitlichen Ansatz des Projekts ab.
Die Projektinhalte des iwb gliedern sich in drei Handlungsschwerpunkte:
Simulationsgestützte Prozessplanung für DED-Verfahren
Charakteristisch für DED-Verfahren ist der sukzessive, hoch-fokussierte Energieeintrag während des Fertigungsprozesses. Dabei spielen einerseits die Prozessparameter, wie die Leistung und die Vorschubgeschwindigkeit, und andererseits die gewählte Bahntrajektorie des DED-Werkzeugs eine entscheidende Rolle für die Ausbildung der mechanischen und physikalischen Eigenschaften des Bauteils. Eine ungünstige Wahl dieser Einflussgrößen kann in lokalen Überhitzungen und unerwünschten Verformungen resultieren. Um kritische Bereiche bereits vor dem Fertigungsprozess zu identifizieren, sollen die DED-Prozesse durch thermomechanische Simulationen abgebildet werden. Temperaturen und Verzüge des Bauteils werden numerisch berechnet, sodass eine Anpassung der Prozessparameter sowie der Bahnführung digital durchgeführt werden kann. Anstatt auf subjektive Erfahrungen zurückzugreifen, sollen die Parameter dabei in einer Optimierungsumgebung ausgewählt werden. Durch diesen Ansatz werden aufwändige Iterationen und damit einhergehende Ausschussteile signifikant reduziert. Eine aussagekräftige Prozesssimulation stellt einen entscheidenden Schritt für die industrielle Etablierung von DED-Verfahren dar.
Inline-Prozessregelung beim Laserauftragschweißen
Ein weiterer Handlungsschwerpunkt ist die Prozessregelung beim Laserauftragschweißen mit koaxialer Drahtzufuhr. Durch diese hochinnovative Prozessvariante, bei der ein drahtförmiger Zusatzwerkstoff innerhalb eines ringförmigen Strahlprofils geführt wird, kann im Gegensatz zur üblicherweise lateralen Drahtzufuhr ein richtungsunabhängiger Materialauftrag ermöglicht werden. Trotz der Vorteile der koaxialen Strahlführung sind neue Fertigungsaufgaben mit einem hohen Aufwand für das Finden geeigneter Prozessparameter verbunden. Durch eine Überhitzung des Bauteils oder eine Abweichung zwischen der Schichthöhe und der Höhenzustellung können insbesondere bei größeren Komponenten Defekte auftreten. Aus diesem Grund soll eine umfassende Prozessüberwachung mittels geeigneter Sensorik in Verbindung mit einer intelligenten Datenverarbeitung implementiert werden. Basierend darauf erfolgt eine Modellbildung sowie der Entwurf einer Mehrgrößen-Prozessregelung, die eine definierte Vorgabe der Schichthöhe sowie der Prozesszonentemperatur ermöglicht. Durch den damit erheblich reduzierten Aufwand für langwierige Parameterstudien sowie die weitere Erhöhung des Automatisierungsgrades soll die industrielle Etablierung des Verfahrens entscheidend beschleunigt werden.
Spanende Endbearbeitung der additiv gefertigten Bauteile
Aufgrund der vielfältigen Möglichkeiten, auch stark belastete Strukturkomponenten durch additive DED-Verfahren herzustellen, kommt der spanenden Nachbearbeitung eine hohe Bedeutung zur Einhaltung von Lage-, Form-, Maß- und Oberflächentoleranzen zu. Der Einsatz von roboterbasierten Nachbearbeitungsprozessen verspricht dabei im Vergleich zu herkömmlichen Bearbeitungszentren enorme wirtschaftliche Potenziale. In diesem Kontext wird ein Strukturmodell des Fräsroboters entwickelt. Auf Basis dieses Strukturmodells soll eine Methodik erarbeitet werden, um die zu erwartenden dynamischen Instabilitäten aufgrund der welligen Oberflächen von DED-Komponenten zu prognostizieren und durch geeignete Prozessplanungen zu kompensieren. Im Rahmen des Forschungsvorhabens soll dazu der Stand der Technik im Hinblick auf die intelligente Prozessplanung und die simulationsgestützte, roboterbasierte Nachbearbeitung substanziell erweitert werden.
Danksagung
Das vorgestellte Vorhaben wird mit Mitteln des Bundesministeriums für Wirtschaft und Klimaschutz (BMWK) unter dem Förderkennzeichen 13IK002L gefördert und vom VDI Technologiezentrum (VDI TZ) betreut. Wir danken dem BMWK sowie dem VDI TZ für die gute und vertrauensvolle Zusammenarbeit.
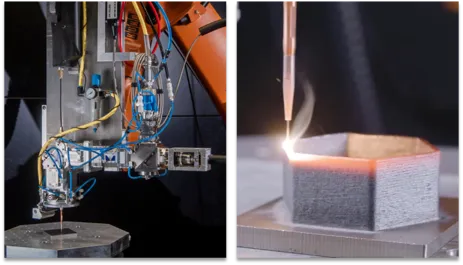
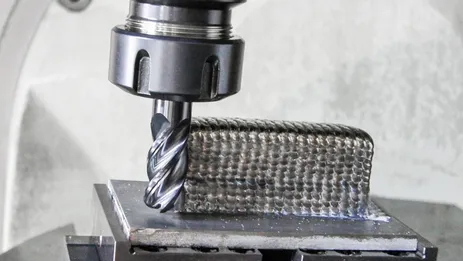
Laufzeit | 01.10.2021 – 30.09.2024 |
Projektpartner | Fritz Automation GmbH, Volkswagen AG, AGCO GmbH, KÖNIG METALL GmbH & Co. KG, Siemens AG, iSYS Software GmbH, Automation W+R GmbH, Boll Automation GmbH, roeren GmbH, applicationtechnology GmbH & Co. KG, Technische Universität München (Institut für Werkzeugmaschinen und Betriebswissenschaften), Precitec GmbH & Co. KG (assoziierter Partner) |
Förderer | Bundesministerium für Wirtschaft und Klimaschutz (BMWK) – Förderinitiative „Digitalisierung der Fahrzeughersteller und Zulieferindustrie“ |
Projektträger | VDI Technologiezentrum |