AdDEDValue – Fully Automated Additive Manufacturing with DED Processes for the Automotive Series Production
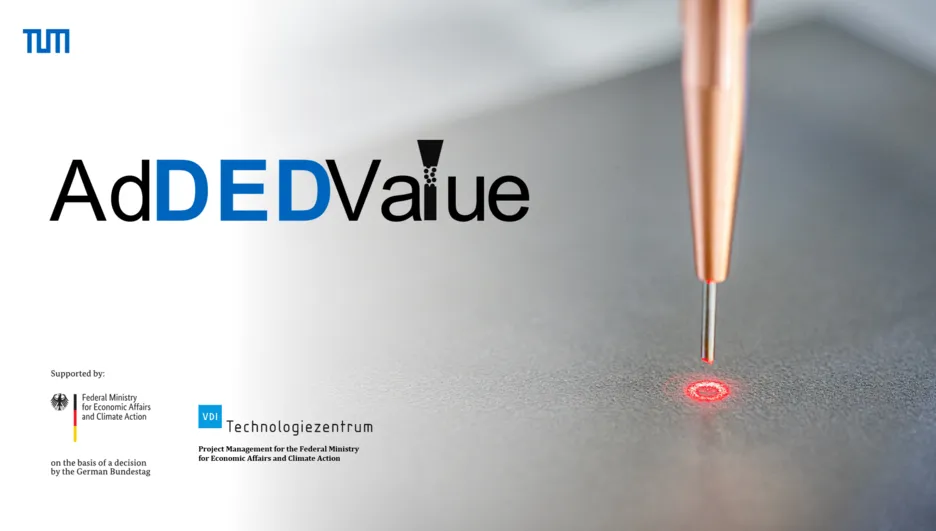
Project overview
The AdDEDValue project aims to achieve an innovation leap in the production lines of the German vehicle manufacturers and the supplier industry. The key technology used for this is metal-based Additive Manufacturing, in which components are produced by repeatedly applying layers using a wire- or powder-based feedstock. In particular, Laser Metal Deposition (LMD) and Wire Arc Additive Manufacturing (WAAM), both so-called DED processes (DED: Directed Energy Deposition), are used. Due to their high achievable deposition rates, these processes represent an economical alternative to established manufacturing processes, not only in single-part production, but also in medium- and large-scale production. The focus of the project lies on the beneficial use of process, plant and component data across the entire manufacturing chain, which is only made possible by the advancing level of digitization in automotive production. As a result, the production systems demonstrated in AdDEDValue will allow for an automated process planning, a real-time process control as well as a reliable and comprehensible quality assurance. An adapted post-processing of the produced components as well as a thorough evaluation of the investigated technologies complete the holistic approach of the project.
The project activities of the iwb are divided into three main fields of action:
Simulation-based process planning for DED processes
A characteristic feature of DED processes is the successive, highly focused energy input during manufacturing. Here, the process parameters, such as the power and the feed rate, as well as the selected path trajectory of the DED tool play a decisive role in the formation of the mechanical and physical properties of the component. An improper choice of these influencing variables can result in local overheating and undesirable deformations. In order to identify critical areas before the manufacturing process, the DED processes will be modeled via thermomechanical simulations. Temperatures and distortions of the component are calculated numerically so that an adjustment of the process parameters as well as the path trajectory can be performed digitally. Instead of relying on subjective experience, the parameters are selected in an optimization environment. Using this approach, extensive iterations and the associated rejects are significantly reduced. A sound process simulation represents a decisive step for the industrial establishment of DED processes.
Closed-loop process control in laser metal deposition
Another main field of action is the closed-loop process control for laser metal deposition with coaxial wire feeding. This highly innovative process variant, in which a wire-based feedstock is guided within an annular beam profile, enables a direction-independent material deposition in contrast to the commonly used lateral wire feeding. Despite the advantages of the coaxial process, new manufacturing tasks involve a great deal of effort for finding appropriate process parameters. Overheating of the component or a deviation between the layer height and the height increment of the tool can cause defects, especially in larger components. For this reason, an adapted process monitoring system will be implemented using dedicated sensor systems in conjunction with intelligent data processing algorithms. Based on this, a system model will be created and a multi-variable closed-loop process control will be designed, which enables a defined specification of the layer height and the temperatures in the process zone. The resulting significantly reduced effort for parameter studies and the further increase in the degree of automation will considerably accelerate the industrial adoption of the process.
Final machining of the additively manufactured components
Due to the wide range of possibilities for manufacturing even heavily loaded structural components using additive DED processes, machining post-processing is of great importance for ensuring compliance with positional, shape, dimensional, and surface tolerances. The use of robot-based finishing processes promises an immense economic potential compared to the use of conventional machining centers. In this context, a structural model of the milling robot is being developed. Based on this structural model, a methodology will be developed to predict the expected dynamic instabilities due to the wavy surfaces of DED components and to compensate them by an adapted process planning. Within the scope of this research project, the state of the art with regard to intelligent process design and simulation-assisted, robot-based post-processing will be substantially expanded.
Acknowledgment
The project presented is funded by the German Federal Ministry for Economic Affairs and Climate Action (BMWK) under the funding code 13IK002L and supervised by the VDI Technology Center (VDI TZ). We thank the BMWK and the VDI TZ for their support and the good and trusting cooperation.
Duration | 01.10.2021 – 30.09.2024 |
Project partners | Fritz Automation GmbH, Volkswagen AG, AGCO GmbH, KÖNIG METALL GmbH & Co. KG, Siemens AG, iSYS Software GmbH, Automation W+R GmbH, Boll Automation GmbH, roeren GmbH, applicationtechnology GmbH & Co. KG, Technical University of Munich (Institute for Machine Tools and Industrial Management), Precitec GmbH & Co. KG (associated partner) |
Funded by | Federal Ministry for Economic Affairs and Climate Action (BMWK) “Digitalization of Vehicle Manufacturers and the Supplier Industry” |
Project management | VDI Technology Center |