The nation-wide online roadmap „Industrie 4.0“ of the German Plattform Industrie 4.0 is online. The Institute of Automation and Information Systems‘ joint project myJoghurt is one of roughly 200 examples from the practice of Industrie 4.0, that are being showcased on the Plattform Industrie 4.0’s online roadmap. It was first introduced by Germany’s Federal Minister of Economy Sigmar Gabriel together with mit further members of the steering committee on November 19th in the context of the national IT-summit in Berlin.
„Germany is leading the way internationally in terms of implementing Industrie 4.0. With the Plattform Industrie 4.0 important impulses could already be provided. However, it is obvious that further steps are required and especially small and medium-sized enterprises will need to be supprted to have coordinated access to the new technologies. Triggering a process of rethinking, inspiring and assisting – that is what the Plattform Industrie 4.0 is meant to achieve in order to accompany enterprises in Germany on their way through the 4th industrial revolution. Results and recommendations of the platform but also an overview of application examples and testbeds should therefore be illustrated with the new online-map and aid in successfully taking this path together“, said Federal Minister of Economy Sigmar Gabriel. At the national IT-summit in Berlin he introduced on November 19th 2015 the virtual roadmap together with Federal Research Minister Prof. Dr. Johanna Wanka and Siemens managing board member Prof. Dr. Siegfried Russwurm (www.plattform-i40.de/I40/Landkarte).
The Institute of Automation and Information Systems (AIS) is setting a good example in the field of Industrie 4.0 in cooperation with other German research institutes. With the prototypical realization of a network of cyber-physical production systems (CPPS) the institute illustrates the possibilities of applications in Industrie 4.0 and supports German companies from different industrial sectors in recognizing capabilities of Industrie 4.0 and adapting them for their own practice. This makes myJoghurt one of roughly 200 examples from the practice of Industrie 4.0 that are being showcased on Plattform Industrie 4.0’s nation-wide online roadmap. The aim is to emphasize the use of digitalization for industrial users. The Plattform Industrie 4.0 provides catalogued application examples of Industrie 4.0 implementations.
The myJoghurt demonstrator shows the prototypical implementation of an architecture for cyber-physical production systems (CPPS) based on the technology of software agents and has been developed with various German research facilities within the group “Theorie und Lehre in der Automatisierungstechnik (TuLAut)” (theory and teaching in automation technology). Locally separated production systems in myJoghurt are connected across the boundaries of individual corporations and subcontractors – both exemplarily represented by the different research institutes – and are able to realize an optimized, distributed production process. Established communication protocols enable continuous vertical integration of machines on a plant’s field-level so that dynamical reconfigurations to current demands and requirements can be made also on this level. At the same time, mobile platforms such as robot controllers can be embedded. Further developments of the demonstrator are currently conducted in the Technical Committee 5.15 „Multi-Agent-Systems“ of the Gesellschaft für Mess- und Automatisierungstechnik (GMA) (Society Measurement and Automatic Control) and are open for further participants and contributions to the demonstrator.
„We are happy to see the Industrie 4.0 demonstrator myJoghurt represented on the Plattform Industrie 4.0’s online roadmap and that we are among the research institutes that are shaping and advancing the digital transition of the German industry together with many other institutes and companies.“ said Prof. Dr.-Ing. Birgit Vogel-Heuser.
At www.plattform-i40.de companies can get tangible insights into the world of Industrie 4.0 – and impulses for their own way towards a digitalized production.
On this website, you can find an overview of the concepts and works of the Institute of Automation and Information Systems of the Technische Universität München regarding Industrie 4.0. The I4.0 demonstrator myJoghurt offers you the opportunity to participate in our research and to implement concepts of Industrie 4.0 yourself!
Resulting from globalization, companies of the manufacturing industry are facing increasing competition. In particular the mechanical and plant engineering is asked to fulfil a series of requirements within Industrie 4.0:
- An ever-increasing number of variants requires mechanisms to control these. Existing knowledge and existing resources have to be utilized, as far as they are feasible regarding efficiency, in order to avoid multiple developments (Re-invent the wheel).
- Reduction of the time to market: customers accept shorter waiting periods. Therefore, efficient development and production in value chains across company boundaries is necessary.
- Product life cycles are getting shorter due to rising innovation pace. Hence, efficient and flexible retooling of production equipment and production lines to new product versions as well as the adaptation of intralogistics within company and the logistics between the companies is critical to success (Vogel-Heuser et al. 2012).
Therefore, solutions are required that provide a great scope for product variants and production variants. Worldwide access to resources and previously unknown production units enables more flexible value chains across company boundaries (Vogel-Heuser et al. 2012).
Influenced by technological change and the utilization of smart sensors, the available amount of data is rapidly increasing in the process and manufacturing industry. These data contains knowledge and additional insights into the production processes and thus provides the basis for flexibility and reuse. Furthermore, the increasing interconnectedness of data allows a more efficient design of value chains.
In Germany, the Internet of Things has been particularly recognized by the logistics enterprises as an approach to information integration of supply chains and production chains based on the Internet. In the US, Cyber Physical Systems (CPS) were proclaimed and fundamentally studied by the Agenda CPS in Germany.
The last of these terms, coined in the area of production, was Industry 4.0. Therein, CPS are i.a. regarded as a technology for upgrading and preparing the production processes for industry 4.0. Using this approach, additional knowledge is acquired through an IT-integration of all available information sources and sinks.
Still there is a disagreement over whether Industrie 4.0 actually represents a revolutionary development, or whether it will instead be an evolutionary technical change. The possibly disruptive character of Industrie 4.0 is predicted due to the suddenly available accessibility to large amounts of data. Yet, due to the high number of operating production plants and their longevity of often more than 15 years, this change will only surface with a time delay for a variety of production facilities.
Production units, which have already been implemented according to the concepts of Industrie 4.0, are called Cyber Physical Production Systems (CPPS). The acatech study AgendaCPS (acatech 2011) defines cyber-physical systems - the basis for Industrie 4.0 - as embedded systems that:
- acquire physical data directly by means of sensors and influence physical processes via actuators
- evaluate and store data as well as use this data to interact in an active or reactive manner with the physical and the digital world
- are interconnected by means of digital networks, both wireless and wired, both locally and globally
- use globally available data and services
- feature a variety of multimodal human-machine interfaces. They provide dedicated facilities for communication and control, e.g. language detection and gesture recognition.
The main technical characteristics of CPPS are grouped into four sub-areas.
Architectural models: For the integration of heterogeneous systems and devices, Service-oriented architectures (Cândido et al. 2011) and Multi-Agent Systems (Colombo et al. 2006) are appropriate solutions. They flexibly interact to exchange information via messages and require minimal standardization. Software agents represent the functionality of the machine and can have a different and proprietary interface features. This is ideal for migrating existing installations.
Communication and data consistency: For industry 4.0 coupling of data from engineering systems, runtime systems and higher-level IT systems is a prerequisite for being able to react flexibly to changes in the production process but also to changing IT systems. Topics such as OPC-UA, AutomationML and semantic descriptions are the basis to achieve this goal.
Intelligent products and intelligent adaptive production units: Based on the product configuration of a customer make the CPPS-production units identify a suitable production process and ensure production of the product, while taking into account product features, cost, safety, reliability, efficiency, time, sustainability etc. If the production needs to be adapted, the production units exchange information autonomously and adapt or evolve in accordance with the adaptation need.
Information aggregation and presentation for humans: Even if all required data is already available, the main challenge is to display this data to humans in a comprehensible way and suitable form. Therefore, the information has to be presented in a suitable form depending on the operator’s individual characteristics, work tasks and role.
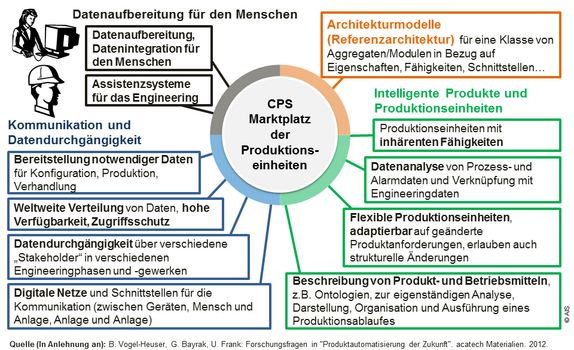
Cândido, G., Colombo, A. W., Barata, J. & Jammes, F. (2011). Service-Oriented Infrastructure to Support the Deployment of Evolvable Production Systems. IEEE Tran. Ind. Inf., 7(4), S. 759–767.
Colombo, A., Schoop, R. & Neubert, R. (2006). An agent-based intelligent control platform for industrial holonic manufacturing systems. IEEE Trans. Ind. Elect., 53(1), S. 322–337.
Vogel-Heuser, B., Bayrak, G. & Frank, U. (2012). Forschungsfragen in „Produktionsautomatisierung der Zukunft“. acatech Materialien, Diskussionspapier für die acatech Projektgruppe „ProCPS - Production CPS“.