Determination of Production-Ready Geometries, Representations, and Interfaces for Modern Gear Manufacturing
Research Topic
Short Title | Geometry and Manufacturing in Gear Calculation |
Start of Project | Q4/2021 |
Funding | FVA-Nr. 241/XVI Research Association for Drive Technology e.V., FVA |
Contact | Dr.-Ing. M. Otto |
Project Description
When designing cylindrical gears, the macro geometry is often determined using optimization calculations or variant calculations. Production-related influences such as grinding allowance or grinding notches in the tooth root are usually not considered due to the lack of parameterizability, but they can certainly influence the optimization result to such a significant extent that it no longer meets the optimization condition. To overcome this dilemma, such influences must be made detectable already in the design phase.
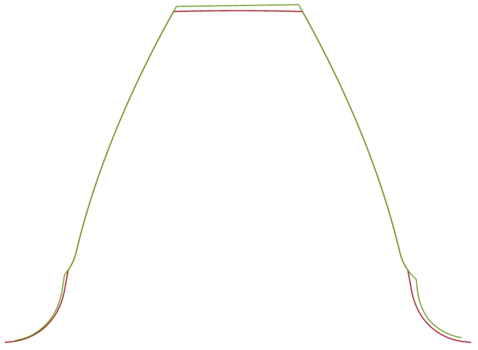
The FVA calculation software for cylindrical gears STplus [Fro16] is used to calculate cylindrical gear stages of any type concerning geometry and load capacity. For this purpose, the tools used are also considered. At present, however, influences from manufacturing processes on the cylindrical gear geometry are not included in detail in the calculation, although this influences the selection of optimal geometry parameters. For example, the grinding allowance can have locally different values. This can lead to areas where there is sometimes not enough allowance for hard and fine machining. Among other things, notches created by the grinding process negatively affect the load-bearing capacity of the gearing in the area of the tooth root. With Wirth [Wir77] or FVA 709 [Pol16], methods are available that can calculate this influence more precisely and thus contribute to a more accurate design.
Precise geometry control is particularly important for the manufacturing of gears. The check dimensions output by the cylindrical gear calculation program up to now (e.g. tooth width or ball dimension) do not take into account free profile modifications or deviations of the pre‑toothing contour due to, for example, hardening distortion or milling deviations. By specifying freely definable profile curves, it is possible to obtain more precise check dimensions from STplus.
In gear manufacturing, the meshing conditions between the tool and the workpiece also play a significant role in the stability of the manufacturing process. The meshing ratios can be optimized by an extended calculation of the meshing between the tool and the workpiece.
Literature
[Fro16] Fromberger, M.: FVA-Nr. 241/XI - Abschlussbericht - Erweiterung FVA-Stirnradprogramm STplus. Abschlussbericht. Frankfurt/Main, Forschungsvereinigung Antriebstechnik e.V. (2016).
[Pol16] Pollaschek, J.; Billenstein, D.; Löpenhaus, C.; Nützel, F. ; Brecher, C.; Rieg, F.: FVA-Nr. 709/I - Heft 1194 - Abschlussbericht - Frei Zahnfußgeometrie - Einfluss der Zahnfußkontur auf die Zahnfußbeanspruchung. Abschlussbericht. Frankfurt/Main Forschungsvereinigung Antriebstechnik e.V. (2016).
[Wir77] Wirth, X.: Über den Einfluss von Schleifkerben oberflächengehärteter Zahnräder auf die Dauerfestigkeit und die Lebensdauer im Zweistufenversuch. Dissertation, TU München (1977).