Department Additive Manufacturing
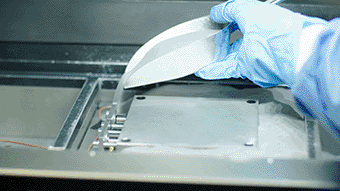
Additive manufacturing is a key technology in the digitalization of production technology. No other manufacturing process enables such a stringent and direct path from the digital CAD model to the physical component. Moulds and tools are no longer required, meaning that additive manufacturing can be used to react flexibly and quickly to changes and enable the economical individualization of mass products. In addition, additive manufacturing opens up previously unknown possibilities for topology optimization and functional integration through the layer-by-layer production of components.
On the research side, the iwb employees are involved in the processing of metallic materials. The process portfolio mainly includes the powder bed fusion of metals using a laser beam (PBF-LB/M) and the wire arc additive manufacturing (WAAM). The equipment at the iwb is completed by innovative in-house systems and systems for processing plastics. The latter are mainly used in teaching or in the production of prototypes. The methodological core competencies of the Additive Manufacturing department include process development, process simulation on various scales and process monitoring. In addition to this, there is expertise in the area of machining post-processing of additively manufactured components, which has been built up together with the Machine Tools department.
Head of Department: Siegfried Bähr
The main research topics
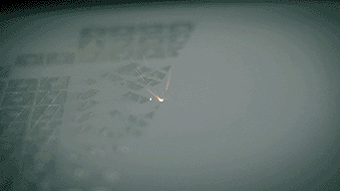
Research Field: Component and process design
In the research field of component and process design, employees deal with overarching issues that arise from the use of additive manufacturing in production systems. The focus here is on the investigation of the fundamental cause-effect interdependencies in additive manufacturing processes using process monitoring methods. In addition, the interactions of the additive manufacturing process with upstream and downstream processes in the process chain are considered. This includes, for example, the adaptation of additive manufacturing processes for the production of medical implants and damping microstructures or the modification of the processes taking into account the process gas influence. In addition, methods of topology optimization for the application-oriented design of components are dealt with.
Research Field Leader: Felix Riegger

Research Field: Component and process simulation
Using numerical methods, the members of the research field of component and process simulation investigate how additive manufacturing processes can be simulated. On the one hand, the application-oriented analysis on the component level, such as the control of component distortion and failure, is addressed. On the other hand, mechanisms on the meso and micro level are investigated - including the formation of shrink lines or the formation of the microstructure. In addition, members of the research field are concerned with the efficient prediction of component structural behavior. The aim is to improve the design of additive components in a process-oriented manner. Another research topic deals with topology optimization, which is used to evaluate the component quality regarding force flow and mass optimization.
Research Field Leader: Hannes Panzer
Find out more about the current projects here.
Equipment in the field of Additive Manufacturing
Systems for arc and wire-based additive manufacturing (Wire Arc Additive Manufacturing, WAAM):
- Fronius CMT-Advanced 4000 welding system
- Fronius TPS 400i welding system
- Kuka KR15/6 six-axis robot with KRC controller
- Six-axis robot Yaskawa Motoman MH24 with two-axis positioner DK250 and control DX200
- Mobile enclosure incl. extraction
Equipment for binder jetting:
- Voxeljet AG VTS 128 test axis
Equipment for ink-jet printing:
- 3D Systems ProJet 3000
Systems for additive manufacturing of plastics:
- Plastic laser-sintering system EOS FORMIGA P 100
- Fused filament fabrication system Ultimaker Original+ (2x)
- Fused filament fabrication system Creality3D Ender 3 (3x)
Devices for process monitoring:
- Chronos 1.4 high-speed camera
- Thermography camera Infratec ImageIR 8300
- High speed thermography camera Flir x6901sc
- 3D digitizer Steinbichler COMET L3D (2M)
Equipment for analytics and evaluation:
- Confocal 3D laser scanning microscope VK-X1000
- 3D profilometer VR-3000
- Tensile testing machine Zwick Roell Z050
- Precision hardness tester LECO LM 100AT
- Macro Vickers hardness tester Wilson VH1150
- Stereo microscope Nikon SMZ1500
- Nikon MM40 reflected light microscope
- Rheometer Malvern Panalytical Kinexus Lab+
- Metallography laboratory with Buhler equipment
Laboratories for Additive Manufacturing
With the innovative future laboratory for Additive Manufacturing at the Institute of Machine Tools and Industrial Management (iwb) of TUM, which was newly established in 2018, the "Additive Manufacturing" Department supports companies in coping with current and future challenges in 3D printing.
On more than 150m² the employees develop solution strategies for the efficient production of tomorrow. The "Additive Manufacturing" team works with you as a project partner to investigate current questions on the individual use of additive technologies - scientifically and problem-oriented.