StabiLO - Process-stable laser structuring of metallic surfaces for large-area joining of 3-D metal structures with fiber-reinforced plastics
Securing a sustainable and resource-efficient mobility in the long-term poses a challenge to the transportation sector. The increasing use of multi-material construction methods requires new production processes in order to economically implement innovative lightweight construction concepts in the future. In this context, the StabiLO project addresses the adhesive joining technology in the production of metal-plastic composites, in which a surface pre-treatment of the metal significantly improves the bond to the fiber-reinforced plastic.
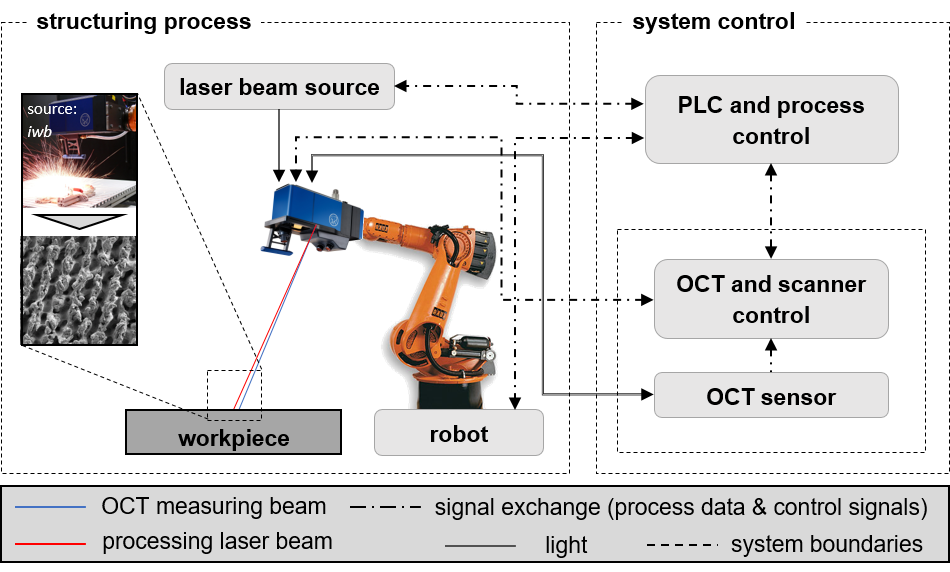
Project details
Project overview
The StabiLO project focuses on the research and the development of a process-stable laser structuring of metallic surfaces for a large area joining of 3-D metal structures with fiber-reinforced plastics (FRPs). Due to an increasing worldwide demand for lightweight, multi-material constructions, innovative manufacturing technologies are required to produce hybrid components with high and consistent quality features. Based on an optimized laser structuring process and a flexible scalable process, an innovative optical sensor concept will be used to realize a process control with the goal of an inline quality assurance. This is expected to result in saving production costs and reducing process times compared to other surface pre-treatments in the production of hybrid components.
Laser structuring of metallic surfaces
Within the scope of the research project, an improved understanding of the process will be established as a basis for a controllable process. A series of statistical tests will investigate the ablation behavior correlated to the process parameters, such as the deflection speed of the scanning optics and the laser power. Considering the parameters of the trajectory, a correlation between the process parameters and the resulting topography will be modeled. In order to enable the structuring of large-area 3-D metallic components, an adapted process control is required, which in turn has an impact on the resulting topography. Therefore, an iterative optimization of the laser structuring process aims to determine an optimal process window. Furthermore, the interactions between the topography and the joining process will be analyzed in order to ensure well-defined mechanical properties for a high-strength composite material. Based on the process investigations, disturbance variables on the process can be identified and, thus, compensation strategies for a control system can be derived.
Inline topography measurement and automation of the data analysis
The technical basis for the laser structuring process is a high-speed scanning optics from Novanta Europe GmbH. As an innovative and flexible tool for an inline topography measurement, optical coherence tomography (OCT) is used during the highly dynamic laser structuring process of metallic surfaces. The integration of the OCT sensor into the scanning optics is one of the technical challenges to be solved with regard to an independent positioning of the OCT measuring beam relative to the processing beam. Based on the developed process control and the optimized scanning optics, a measurement strategy adapted to the structuring process can be derived and, thus, an inline quality assurance can be realized. With a sampling frequency of up to 70 kHz and the resulting amount of measurement data generated in this context, an automated data processing needs to be developed to realize a closed-loop control system. Methods based on artificial intelligence are a suitable method in the evaluation of OCT measurement signals. In addition, synchronized, low-latency and high-performance interfaces between the peripheral components are crucial for a fast sensor data processing.
Intelligent control of the laser-based structuring process
In order to enable the use of the developed technology in an industrial series production, a high-performance control system is required to implement an inline quality assurance. The evaluated OCT sensor signal serves as an input variable for the control system. Deviations between the actual and the target topography can be caused by heated system components or by a varying clamping of the workpiece. Indicated by fluctuations in the measurement signal, the deviations can be compensated by controlling the appropriate process variables, e.g., the laser power. Therefore, suitable control concepts need to be tested and evaluated with regard to further requirements. The process control will then be developed and implemented on a digitization platform by Grenzebach Digital GmbH. The platform also serves as a central interface for the peripheral components involved.
Scaling of the joining process for an industrial application
A demonstrator component will be used to evaluate the developed structuring process and the thermal joining process. The functional demonstrator will be implemented together with Airbus Helicopters Germany. For an optimal design of the joining process, experimental investigations are carried out to analyze the bonding strength of the metal with the FRP. In addition, the focus is on scaling the joining process in order to be able to produce high-quality hybrid components, including a minimum of air inclusions. By varying the overlapping areas of the metal and the FRP, numerous different application cases will be covered.
Acknowledgements
The iwb would like to thank the Bavarian Research Foundation for funding this research project. The responsibility for the content of this publication belongs to the author.
Informationen
Duration | 01.03.2021 – 29.02.2024 |
Project partner | Novanta Europe GmbH, Wackersdorf; Grenzebach Digital GmbH, Augsburg; Airbus Helicopters Deutschland GmbH, Donauwörth; Institute for Machine Tools and Industrial Management of the Technical University of Munich |
Funded by | Bavarian Research Foundation (BFS) |