Motivation:
Driven by stricter legal requirements and the desire for a production process that is not harmful to health or the environment, inorganically bonded cores are increasingly being used in light metal foundries. In contrast to organically bonded cores, this produces significantly less harmful emissions during casting. However, new technical challenges are also emerging. One disadvantage of inorganically bonded molding material is that the de-coring process is significantly more complicated and results in more significant stresses on the component. Also, gas-development and hot-deformation while casting differ considerably from current models.
From current projects:
- Analysis of core shooting parameters influence on core properties
- Microstructure simulation of inorganically bonded molding materials
- Development of a fracture model for de-coring simulations
Objective:
The main objectives are to predict molding material and process properties based on physical and statistical models.
Competences of the Chair:
1. Characterization of Molding Materials (see also "Material Characterization in Founding")
- Tensile stress
- Elongation at break
- Gas permeability
- Casting defects
2. Core Shooting Tests and Influence Analyses with different Binder and Sand Combinations
3. Qualification of Hot Deformed Molding Materials
Picture Gallery:
For the core competence, freeform bending, the chair is equipped with a freeform bending machine from Neu GmbH. The use of up to 6 CNC axes enables more simple bending of asymmetrical profiles or thin-walled round tubes (also with mandrel) to form contours that previously could only be produced with considerable effort. The bending area's material structure is retained, which ensures high formability.
With freeform bending with a moving die, the chair expands its research portfolio to include a further production option. The research focuses on producing complex profile components and further developing in-line process control during bending.
Research Content Includes:
- Freeform Bending of Profiles and Tubes
- Specified Tooling Standards
- Investigation of Material Properties and their Changes due to the Bending Process
-
Advanced Process Control concerning Material Properties
Photo Gallery:
The Philosophy at utg:
Excelent Testing Technology → Customized Evaluation Methodology → Continuois Validation
Testing Technology:
1. Uniaxial Tensile Test according to DIN EN ISO 6892
- Tactile or optical length and width measurement
- Different strain rates possible
- Temperature control in the range -60°C ... 900°C possible
2. Hydraulic Cupping Test (Bulge Test) accoring to DIN EN ISO 16808
- Optical strain measurements
- Different cupping speeds possible
3. Further Tensile Tests under different Load Types
- Tensile Test under approximately plane strain condition
- Tensile Test under shear
4. Determination of the Forming Limit accoring to DIN EN ISO 12004-2
- Nakajima process or Macainiak process
- Production of defined pre-strains (homogeneous, planar area minimum Ø 80 mm)
5. Defined Post-Expansion of Pre-Stretched Specimens for the Generation of Non-Proportional Load Parts
6. Representation of almost Arbitrary Non-Proportional Load Paths in a Modified Crucifrom Test
Evaluation Methodology:
Determination of required characteristic values of the calibration of models for the numerical description of material behavior of sheet materials:
1. Modeling of elastic meterial behavior
2. Modeling of elastoplastic material behavior
- Different yield point models
- Strengthening behavior of materials
3. Determination of relevant process limits for forming
- Determination of forming limit changes for nearly linear strain paths according to DIN EN ISO 12004-2
- Calibration of the General Froming Limit Concept (GFLC) for the evaluation of non-poroportional load paths
Validation:
1. Execution of special tests with complex strain conditions subjected to low friction influences with a quasi-continuous optical strain measurement
2. Simulative mapping of the tests using existing material models
3. Evaluation of the simulation and validation of the material description applied
Photo Gallery:
In addition to general research work in forming technology, the chair has specialized in the field of shear cutting for many years and can draw on a wealth of experience.
With the Experimental Technology Available at the Chair and the Know-How Developed, the following Processes are Possible:
- Production of shear-cut specimens of various geometries with sheet thicknesses from 0,1 mm to 10 mm with a variety of process parameters such as the cutting gap or the cutting edge geometry
- Various process variants such as fine blanking or sheaving possible
- Processing of elecrical, steel, aluminium, copper, bronze, hybrid, and plastic sheets
- Wear investigations with variation of the oiling, sheet metal material, tool stiffness, thermocurrent, active element material, and coating
- Production of specimens to identify the fatigue strength of shear cut edges
- Investigation of embossing, clinching, and bending operations, including in combination with shear cutting operations
- Experimental determination of the edge crack sensitivity of shear-cut samples
Established Evaluation Methods at the Chair:
Determination of required characteristic values for the evaluation of the cut surface properties, the wear behavior, and the behavior of shear-cut edges in subsequent operations or the application:
- Quantification of active element wear, adhesion, and flash formation
- Measurement of process forces
- Measurement of cutting surface parameters
- Macro-hardness and micro-hardness testing
- Identification of parameters for the consideration of edge crack behavior in the simulation
- Identification of the electromagnetic properties of shear cut electrical sheets
Photo Gallery:
The Chair of Metal Forming and Casting investigates the stamping of electrical sheets in two projects funded by the German Research Association. The topics "Processing of Electrical Sheet Thin Strips into Electromagnetic Components" and "Targeted use of Residual Stress in Electrical Sheets to Increase Energy Efficiency" analyze production processes' optimization to increase electrical drive efficiency.
Magnetic fields are generated in electrical machines to convert electrical energy into kinetic energy. Therefore, the magnetic properties of the electric drive's main component, the so-called electrical sheet, are crucial for its efficiency. We have shown that the electrical sheet's manufacturing process influences its magnetic properties in the past. This characteristic is mainly due to residual stresses that arise during production. Shear cutting of electrical steel induces residual stresses near the shear influence zone, reducing the electrical drive's efficiency. In contrast, the sheet's targeted embossing allows the induction of residual stresses, enabling the magnetic flux's precise guidance to improve the motor cores' magnetic properties.
When shear-cutting the electrical sheet, the process parameters significantly influence the processed material's magnetic properties. Optimized processes minimize losses and the required electricity by using small cutting gaps and sharp cutting active elements. Above all, tool wear is a primary influence for deteriorated magnetic material properties. The research project aims to provide optimized process parameters for the industry.
In contrast to shear cutting's negative effects, residual stresses are used explicitly as magnetic flux barriers due to embossing. Conventional flux barriers are designed as cutouts and enable precise magnetic flux guidance. However, this is accompanied by a reduction in the rotor design's mechanical strength. We are researching an alternative flux barrier concept to operate electric drives at higher speeds. Since residual stresses fundamentally degrade magnetic material behavior, embossing locally increased residual stresses act as flux barriers. Our studies focus on different embossing strategies to achieve maximum energy efficiency for selected electric drives.
Photo Gallery:
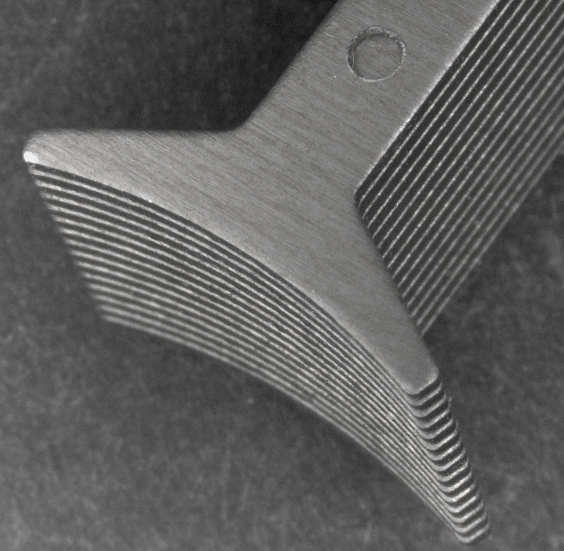
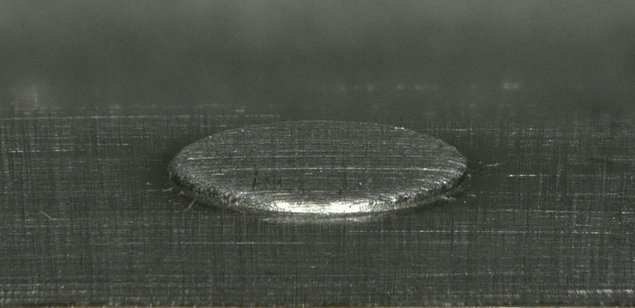
Continuous and composite casting is one of the chair's research focal points. These processes offer great potential for improvement in foundry production. Accordingly, a scientific breakthrough in the topic is of great interest.
The following aspects are a motivation for the research at the chair:
1. Load-adapted lightweight material combinations
- Hybrid structures
- Complex property profiles
- Cost-optimized use of materials
2. Process chain shortening
- Integration of joining operations into the casting process
- Elimination of intermediate process steps, e.g., chemical cleaning, heat treatment
3. Resource efficiency
4. Utilization of thermal and latent energy for the compound generation
- Material efficiency
- Time savings through process chain shortening
5. Potential of material-bonded composite formation concerning load-bearing capacity and further processability
6. Design and modification flexibility
Research content at the chair:
1. Experimental and simulative process investigation
- Continous casting
- Composite casting
- Incremental casting
2. Composite casting analysis
- Melting and recrystallization mechanisms
- Diffusion processes
- Wetting behavior
- Microform closure
Photo Gallery:
Liquid metal jetting is an additive manufacturing process in which droplets of liquid metals are deposited onto a build platform. To investigate the process, a test stand was developed at utg that can process aluminum alloys, copper alloys and salts. The salts are used as support material.
Research topics in the area of Liquid Metal Jetting are:
- development of the processing of new materials
- characterization of printed samples
- numerical simulation of the printing process