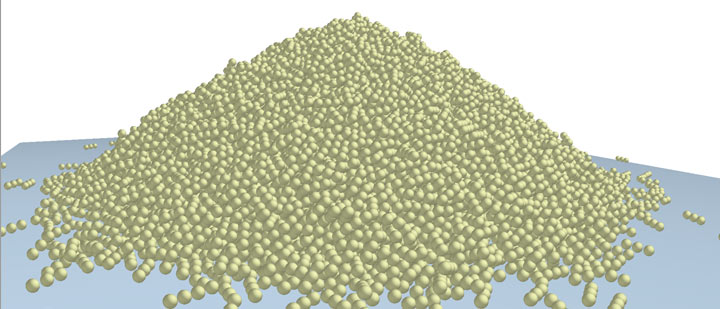
DEM-Schüttgutdatenbank: Verfahren zur Kalibrierung von DEM-Materialmodellen
Verkürzte Produktlebenszyklen, hohe Anforderungen an die Produktqualität und vor allem steigender Innovationsdruck haben bereits in der Vergangenheit dazu geführt, dass die Funktionen neuer Produkte bereits während der Entwicklung verifiziert und unterschiedliche Varianten bewertet werden müssen.
Dieser Herausforderung wird im industriellen Umfeld häufig mit Methoden der numerischen Simulation begegnet. Die rasche Entwicklung auf dem Gebiet der Informationstechnologie hat diesen Trend in den letzten Jahren durch die Bereitstellung leistungsfähiger Rechnersysteme weiter vorangetrieben, sodass auch für aufwändige Simulationen meist handelsübliche Workstations ausreichen.
In der Fördertechnik wird zumeist auf die Finite-Elemente-Methode (FEM), die Mehrkörpersimulation (MKS) und die Diskrete-Elemente-Methode (DEM) zurückgegriffen, um den Konstruktions- und Entwicklungsprozess effektiv zu unterstützen. Die DEM wird dabei insbesondere zur Simulation von Schüttgütern und Auslegung von Fördergeräten eingesetzt.
Da die DEM erst seit circa einem Jahrzehnt in der Industrie Verbreitung findet, existieren – beispielsweise im Gegensatz zur FEM – noch keine einheitlichen Standards zur Bestimmung von Materialmodell-Parametern. Es gibt verschiedene best practices, welche jedoch nicht immer mit gleichem Erfolg auf leicht und schwer fließende Schüttgüter angewendet werden können.
Dieses Problem ist auf zwei Hauptursachen zurückzuführen.
Die erste Ursache bezieht sich auf die Messung von Schüttgut-Eigenschaften. So kann z.B. der Schüttwinkel (Böschungswinkel), eine zentrale Größe von Schüttgütern (vgl. Abb. 1), bereits durch die Auswahl des Messverfahrens beeinflusst werden. Existierende Standards zur seiner Messung beziehen sich auf leicht fließende, feinkörnige Güter und sind deshalb für stückige und kohäsive Materialien im Allgemeinen nicht geeignet.
Die zweite Ursache ist die Ermittlung der DEM-Materialmodell-Parameter. Üblicherweise werden die Materialparameter eines Schüttguts, z.B. der Reibungskoeffizient zwischen Partikel und Wand, auf mikroskopischer Ebene gemessen. Durch die Materialmodell-Parameterisierung auf Basis dieser mikroskopischen Eigenschaften kann jedoch nicht garantiert werden, dass sich das makroskopische Fließverhalten von tausenden Partikeln so einstellt, wie man es in Messungen beobachtet.
Wegen der Diskrepanz zwischen mikroskopisch gemessenen und makroskopisch beobachtetem mechanischen Verhalten bei der Diskrete-Elemente-Modellierung von Schüttgütern müssen die virtuellen Materialien einem Kalibrierungsprozess unterzogen werden. Dabei modelliert man die Materialtests mittels DEM und ändert, ausgehend von den mikroskopischen Eigenschaften, die Materialparameter so lange ab, bis sich das beobachtete Verhalten einstellt. Als Ergebnis steht sodann ein Materialparametersatz für die DEM zur Verfügung.
Welcher Parameter in welcher Größenordnung verändert werden muss, um die Messergebnisse simulativ zu reproduzieren, legt ein DEM-Anwender fest. Je nach Erfahrung des Anwenders kann dieser Prozess sehr langwierig sein und garantiert nicht, dass wirklich der beste Parametersatz gefunden wurde. Zudem liegen Wechselwirkungen zwischen Materialparametern vor und manche Parameter wirken sich auf mehr als nur eine Messgröße aus. Beispielsweise beeinflusst die Rollreibung von Partikel zu Partikel neben dem Schüttwinkel auch die Schüttdichte. Dies sind Gründe, warum es schwierig ist, während des Kalibrierungsvorgangs den Überblick zu behalten.
Zunächst wird eine Auswahl an zu untersuchenden Schüttgütern getroffen und Methoden zur Messung von wichtigen Schüttguteigenschaften, wie Schüttdichte, Schüttwinkel, Partikelgrößenverteilung und Gleitwinkel, ausgewählt.
In einem nächsten Schritt werden die Partikelgrößenverteilungen analysiert und geometrische Modelle der Schüttgutpartikel erstellt. Dabei muss ein Kompromiss zwischen der Abbildungsgenauigkeit und der Effizienz der DEM-Berechnungen eingegangen werden, da durch die maßstäbliche Modellierung unzumutbar lange Berechnungszeiten folgen würden. Die Partikelgröße wird für die DEM deshalb hochskaliert.
Die Versuchsaufbauten aus dem ersten Schritt werden sodann mittels einer open-source DEM-Software modelliert und fortan für die Entwicklung eines Kalibrierverfahrens für die Kalibrierung der Materialparameter eingesetzt.
Der Kalibrierungsprozess soll im Rahmen dieses Forschungsprojekts automatisiert werden. Dies wird durch den Einsatz von numerischer Optimierung angestrebt. Obwohl dadurch die Anzahl der durchzuführenden DEM-Simulationen ansteigt, soll die Robustheit des Optimierungsverfahrens die Qualität der Materialmodelle verbessern. Zudem soll so das Versuch-und-Irrtum-Verfahren, welches bei der Kalibrierung bisher weit verbreitet ist, durch eine methodische Prozesskette ersetzt werden. Gerade wenn ein DEM-Materialmodell auf verschiedene Messgrößen getrimmt werden muss, ist ein automatisierter Prozess effektiver als die Parametereinstellung durch einen Menschen.
- Andreas Schorr GmbH
- Bühler GmbH
- FLSmidth Wadgassen GmbH
- ThyssenKrupp Resource Technologies GmbH
- Vollenda-Werk GmbH
Das IGF-Vorhaben 18371 N/1 der Forschungsvereinigung Intralogistik/Fördertechnik und Logistiksysteme e.V. (FG IFL) wird über die AiF im Rahmen des Programms zur Förderung der industriellen Gemeinschaftsforschung und -entwicklung (IGF) vom Bundesministerium für Wirtschaft und Technologie aufgrund eines Beschlusses des Deutschen Bundestages gefördert.