The rapid changes in information technology and increasing computing power offer new possibilities for automation. Today's highly automated manufacturing requires agile material flow systems. Within logistics, which is characterized by increasingly complex structures and processes as well as shorter reaction times, self-controlling, intelligent systems are becoming increasingly important. The autonomization of transports on the factory site, which are not only automated but also intelligently controlled, is the subject of current and future research and development. This is sometimes due to increasing cost pressure, increased transport volumes and the need to adapt material flow systems. The current, largely manual work steps involved in transporting materials on the plant premises are a considerable cost factor in logistics. In order to reduce these costs, control the increasing transport volumes intelligently and ensure the adaptively of the systems, the implementation of autonomous transport systems on the plant premises is a possible solution. Autonomous systems tend to have the following advantages: they are standardized and more efficient than manual material flow systems and have the ability to be adaptive, flexible and self-learning compared to automated systems.
Automated transport systems (AGVs) are already increasingly being used within the factory buildings. The internal material flow, however, is not only limited to the transports within the halls, but also considers the transports outside the hall on the factory premises. The demands placed on AGVs in outdoor areas are significantly higher than in indoor areas. For example, crossing level crossings or adapting priority rules poses a considerable challenge. In addition, the AGV must be able to drive safely even in different weather conditions and ground conditions and transport the goods protected. The ability to react robustly and independently to unforeseeable events and situations is the core capability of an autonomous system. Therefore, in this thesis the term autonomous is clearly distinguished from the term automated. In order to fully exploit the technical and economic potentials of autonomous transport systems, a method for the implementation of autonomous transport systems in outdoor areas will be developed within the framework of this research work.
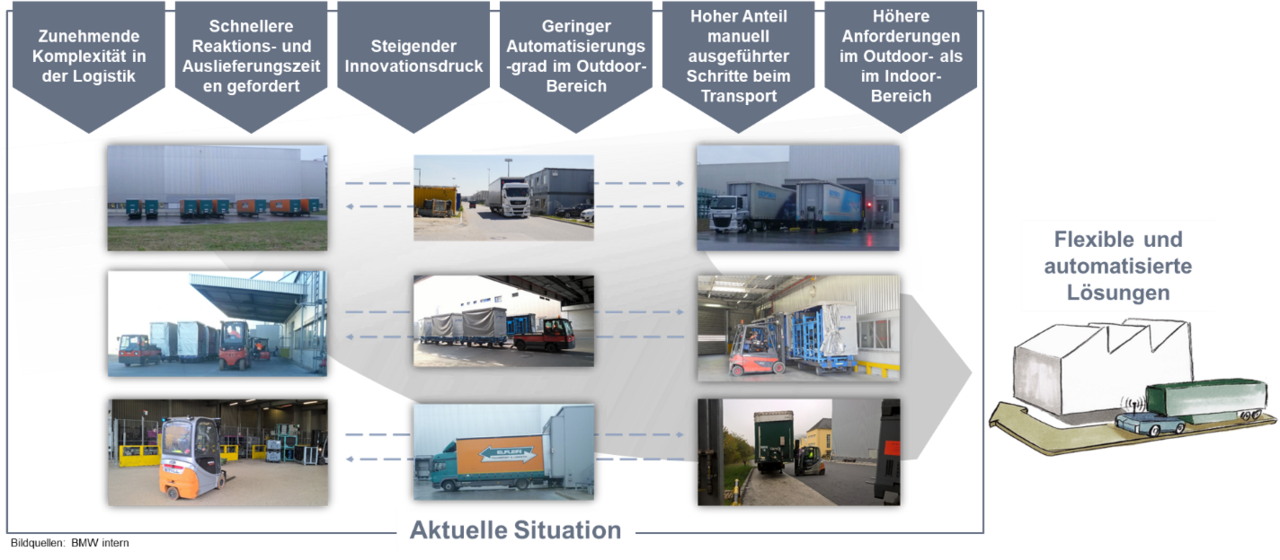
The aim of the research work is the development of a method for the flexibilization and optimization of transports on the factory premises through the integration of autonomous transport systems into existing structures and processes. The effort towards autonomous systems, which have the ability to act self-determining and independent without human intervention, is great. However, there is a lack of a method that can be applied for the integration of autonomous transport systems. In addition, automated transport systems are considered and used primarily in indoor areas, but not autonomous systems in outdoor areas. Therefore, in this research work, requirements are to be defined on the basis of the currently existing transport processes on the factory premises and reference processes are to be derived from them. These will be evaluated with regard to technology, process and control and then converted into a standardized method for the integration of autonomous transport systems in outdoor areas. The reference processes form the target processes and thus, together with the requirements, the basis of the method. A validation of the method on the basis of a real use case can point out alleged strengths and weaknesses, which flow afterwards also into the method. It is to be based on the current state of science and technology, in which autonomous transport systems in the indoor area as well as automated transport systems in the outdoor area are already considered.
The research project is divided into ten work packages. First, the state of the art of technology and science will be analyzed by means of expert interviews. This is followed by an actual survey of the transport processes on the plant site. With the help of a weak point and potential analysis, the actual processes are evaluated and requirements and required functions are derived. The analyzed and collected information and data is then summarized in a requirements profile. In the next step, the necessary technology systems and their environment are selected and evaluated. Based on the requirement profile and the technology systems, the reference processes for the automation of transports are derived. The resulting framework conditions and structures are the basis for the development of the method for the integration of autonomous transport systems on the factory site. The research project concludes with a demonstrative implementation of the developed method in the real logistics processes of the BMW Group.