ProzessLog
Entwicklung einer Methode zur standardisierten, aufwandsarmen Aufnahme und intuitiven Visualisierung innerbetrieblicher logistischer Prozesse unter Berücksichtigung der verwendeten Technologien
Die Logistik, insbesondere die Intralogistik, stellt die zeit- und mengenrichtige Versorgung der Produktion sicher und ist in den letzten Jahren immer mehr zum Wettbewerb bestimmenden Faktor geworden. In Zeiten rascher Produkt- und Innovationszyklen sieht sich die Logistikplanung mit der Aufgabe konfrontiert, Prozesse in immer kürzerer Zeit anzupassen oder neu zu entwickeln.
Die Basis für eine Optimierung beziehungsweise Planung von Logistikprozessen bildet dabei ausschließlich eine ganzheitliche Prozessaufnahme unter Berücksichtigung von Material- und Informationsfluss sowie der eingesetzten Techniken, da diese sich gegenseitig bedingen. Nur so können die für die spätere Prozessgestaltung notwendigen Prozessdaten vollständig in ihrem Zusammenhang erfasst und die richtige Datenbasis als Ausgangssituation geschaffen werden. Die Prozessaufnahme ist somit ein Kernelement der Logistikplanung und entscheidet als Grundlage für die Prozessmodellierung über den Erfolg von Optimierungs- und Anpassungsmaßnahmen.
Aktuell existiert keine einheitliche, allgemein verständliche Methode für alle Unternehmenshierarchien, die eine ganzheitliche Prozessaufnahme unter Berücksichtigung von Material-, Informationsfluss und eingesetzter Technik ermöglicht. Das ist jedoch erforderlich, da einzelne Vorgänge des Materialflusses durch Informationen ausgelöst werden und ihrerseits wiederum Informationen, bspw. in Form von Statusangaben, erzeugen.
Bestehende Methoden fokussieren im Regelfall die Prozessmodellierung und sind auf Grund ihrer Komplexität und der dadurch notwendigen tiefen Methodenkenntnis für die reine Prozessaufnahme nur bedingt geeignet. Für die Erfassung des Prozesses ist jedoch ein zeiteffizientes, leicht verständliches Vorgehen, das eine Prozessdiskussion mit allen Beteiligten vor Ort ermöglicht, eine elementare Voraussetzung. Der Einsatz von Methoden, die ihren Fokus nicht im Bereich der Prozessaufnahme, sondern in nachgelagerten Phasen der Planung haben, resultiert dadurch oftmals in einer unvollständigen beziehungsweise fehlerhaften Ersterfassung der IST-Situation, wodurch zeit- und kostenintensive Iterationsschleifen notwendig werden. Besonders für kleine und mittelständische Unternehmen (KMU), die nur über sehr begrenzte Kapazitäten verfügen, ist eine intuitive, verhältnismäßig aufwandsarme Prozessaufnahme daher von wirtschaftlicher Bedeutung.
Des Weiteren betrachten zahlreiche Methoden entweder speziell einen Geschäftsbereich oder lediglich den Material- und/oder Informationsfluss. Für eine ganzheitliche Prozessaufnahme ist es aber zwingend erforderlich, auch die dabei zum Einsatz kommende Technik zu berücksichtigen, von der in der Logistik eine Vielzahl bspw. für Transportaufgaben, die Materialflusssteuerung, Informationsverarbeitung oder Identifizierung (z. B. RFID) eingesetzt wird und die wesentlich für deren Effizienz ist. Insbesondere AutoID-Techniken wie RFID halten auf Grund der Verknüpfung von Material- und Informationsfluss und der damit verbundenen Prozesstransparenz verstärkt Einzug in die Logistik, erfordern jedoch die Aufnahme spezifischer Prozessinformationen.
Wegen einer fehlenden ganzheitlichen Aufnahmemethode haben sich insbesondere bei großen Firmen individuelle Prozessaufnahmewerkzeuge bzw. -methoden ohne Standardisierungsanspruch etabliert. Bei KMU hingegen erfolgt die Prozessaufnahme in der Regel oft auf Basis des Erfahrungswissens des jeweiligen Planers und ohne Methodenunterstützung. Aber nur mit einer Methode, die unabhängig von der untersuchenden Person (subjektunabhängig), der Untersuchungssituation (situationsunabhängig) und zufälligen Zuständen des Forschungsobjekts (zustandsunabhängig) ist, können die Datenqualität sichergestellt und das im Rahmen von Projekten zur Verfügung stehende Zeitfenster eingehalten werden. Deshalb profitieren von einer standardisierten Aufnahmemethodik insbesondere KMU.
Der Bedarf für eine neuartige, standardisierte Prozessaufnahmemethode als Voraussetzung für eine gesamtlogistische Prozessbeurteilung wird auch in Anbetracht der auf Grund fehlender Überarbeitung zurück gezogenen VDI-Richtlinie 3300 deutlich. Vor diesem Hintergrund fand eine Zusammenarbeit mit dem VDI statt.
Das Ziel des Forschungsprojekts war die Erarbeitung einer allgemein gültigen Methode zur ganzheitlichen Aufnahme innerbetrieblicher Logistikprozesse als Basis für eine spätere Prozessmodellierung und -simulation. Neben dem Material- und Informationsfluss werden auch die eingesetzten Ressourcen berücksichtigt. Dazu wurden sowohl für den Materialfluss als auch für den Informationsfluss intuitive Prozessbausteine definiert, die durch einfache Symbole dargestellt und mit klaren Attributen beschrieben werden können. So können Prozesse einfach vollständig dokumentiert und noch vor Ort mit den Prozessbeteiligten diskutiert werden, um Optimierungspotentiale ableiten zu können. Zudem lässt eine derartige Methode eine einfache Bewertung der dargestellten Prozesse nach bestimmten Kenngrößen (z.B. Prozesszeit, Häufigkeit, Kosten) zu, indem Ist- und Soll-Prozesse auf Grund eines einheitlichen Detaillierungsgrades direkt miteinander verglichen werden können. Ein weiteres Ziel lag in der Unterstützung des Anwenders bei der Beschreibung von Optimierungspotenzialen durch die Methode.
Zunächst wurden anhand von Fachliteraturrecherchen und verschiedenartigen innerbetrieblichen Logistikprozessen der Forschungspartner grundlegende Vorgänge und durchgeführte Tätigkeiten in einem logistischen Prozess identifiziert und beschrieben. Dabei wurde zwischen Material- und Informationsfluss unterschieden und die eingesetzten Ressourcen identifiziert. Ebenso wurde ein Vorschlag zur Gliederung innerbetrieblicher Logistikprozesse erarbeitet (siehe Abbildung 2). Diese soll den Anwender bei der Fokussierung des Betrachtungsgegenstandes unterstützen.
In einem weiteren Schritt wurden verschiedene Methoden für die Aufnahme und Darstellung logistischer Prozesse recherchiert. Hierzu wurden neben einschlägiger Fachliteratur Prozessanalysten im Rahmen einer empirischen Erhebung befragt. Die auf diese Weise ermittelten Methoden (siehe Abbildung 1) wurden in einem weiteren Schritt bewertet, um deren Stärken und Schwächen in einem Benchmark, das die Grundlage der neuen Methode ist, zusammenzufassen. Zu diesem Zweck wurde auf Basis der zu dokumentierenden Prozessdaten aus dem vorangehenden Schritt ein hierarchischer Zielkriterienkatalog entwickelt, anhand dessen die verschiedenen Methoden hinsichtlich der Darstellung eines einheitlichen Musterprozesses beurteilt wurden. Im Einzelnen wurde die Zielerfüllung hinsichtlich der Darstellung der Prozessleistung, Prozesslogik, Prozessverständnis und insbesondere Prozessgestaltung beschrieben.
Aufbauend auf den zuvor durchgeführten Arbeitspaketen wurden die Grundlagen der neuen Prozessaufnahmemethode definiert. Diese stellt ein zweistufiges Vorgehen dar. In der ersten Stufe wird der betrachtete Prozess grafisch in der Prozessskizze, die für jeden Teilprozess den Material- und Informationsfluss als miteinander verbundene Swimlanes darstellt, abgebildet. Hierfür wurden sowohl für Material- als auch für den Informationsfluss logistische Grundfunktionen (siehe Abbildung 3) erarbeitet, die durch spezifische Attribute beschrieben und bewertet werden können. Diese werden gemäß der Prozesslogik in der Prozessskizze platziert und miteinander verkettet. In einer dritten Swimlane werden die dabei zum Einsatz kommenden Ressourcen sowie Hilfsprozesse, die nicht das eigentliche Materialflussobjekt zum Gegenstand haben (z.B. Leerfahrten), dargestellt. Jede Grundfunktion wird mit einem klaren Symbol dargestellt, ist eindeutig nummeriert und kann im Sinne eines besseren Prozessverständnisses über einen Kurztext grundlegend beschrieben werden.
Der Prozessaufnahmebogen ist die zweite Stufe der Prozessdarstellung. Darin werden die Grundfunktionen mit ihrer eindeutigen Nummer aufgenommen und deren Eigenschaften über die spezifischen Attribute beschrieben. Die Attribute können sowohl vor Ort an der jeweiligen Stelle im Prozess als auch im weiteren Verlauf der Prozessaufnahme im Rahmen von Expertengesprächen detailliert werden. Schlüsselattribute, die für die Bewertung der Grundfunktionen und die Beurteilung von Optimierungspotenzialen wichtig sind (z.B. manuelle, mechanisierte, automatische Durchführung) werden anhand klarer Symbole bereits in der Prozessskizze vermerkt. Durch die Attribute können Prozessbewertungen vorgenommen werden, um Soll- und Ist-Prozesse einander gegenüberzustellen.
Auf Grund der klaren und einfachen Verknüpfung zwischen Material- und Informationsfluss eignet sich die Methode auch zur Darstellung RFID-unterstützter Prozesse. Die dabei relevanten Prozessrandbedingungen können durch die Attribute beschrieben und mögliche Optimierungspotenziale durch Checklisten für die einzelnen Grundfunktionen hinterlegt werden. Deshalb unterstützt der VDI eine Überarbeitung der VDI-Richtlinie 4472, die aufbauend auf der Methode ein Werkzeug zur Darstellung RFID-gestützter Prozesse beschreiben soll.
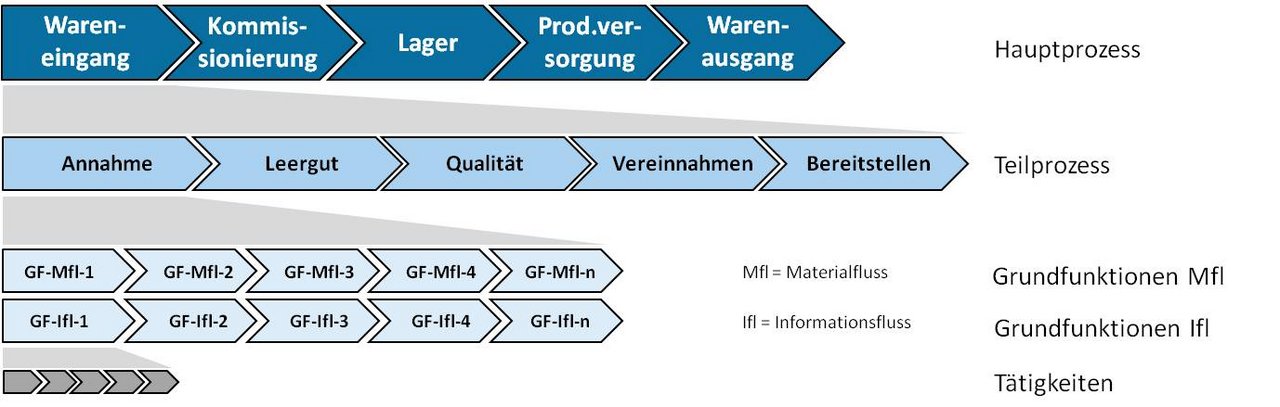
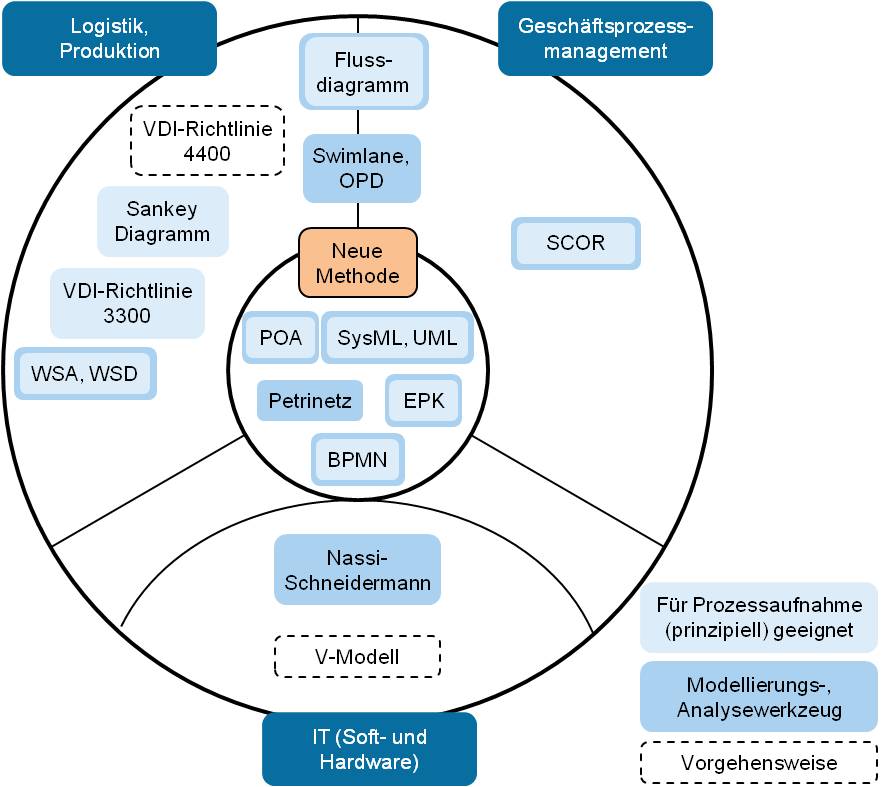
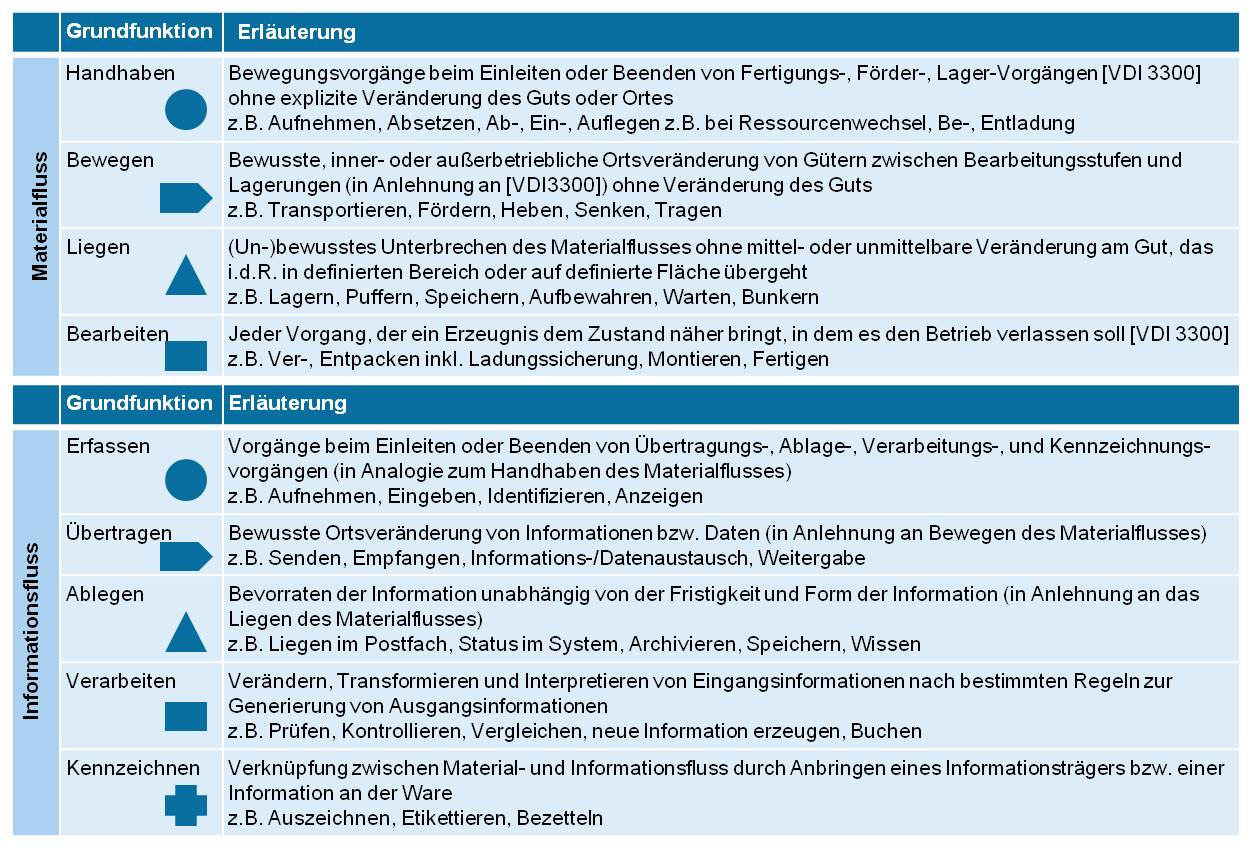
- Business Launch Support Grinninger
- CIM GmbH
- CNX Consulting Partners
- Etifix GmbH
- Gebrüder Jäcklin GmbH
- Jungheinrich AG
- Lindner AG
- Logistik Consulting Allgayer
- W. & M. Schenk GmbH
- Schmidt-Seeger GmbH
- Süß MicroTec AG
- trilogIQa
- Verein Deutscher Ingenieure e.V.
Das IGF-Vorhaben 16187 N / 1 der Forschungsvereinigung Bundesvereinigung Logistik e.V. (BVL), Schlachte 31, 28195 Bremen wurde über die AiF im Rahmen des Programms zur Förderung der industriellen Gemeinschaftsforschung und - entwicklung (IGF) vom Bundesministerium für Wirtschaft und Technologie aufgrund eines Beschlusses des Deutschen Bundestages gefördert.