In recent years, in-plant milkruns have increasingly been used across all industries as a means of transport for internal production supply. They enable the bundled transport of different materials to different places of demand on one journey. The highly cyclical supply synchronizes logistics and production. In-plant milkrun systems are thus a central component of the lean production philosophy.
The main tasks of the planning of in-plant milkrun systems are the definition of corresponding routes (routing) and departure times (scheduling). Currently, this is usually done on the basis of average transport requirements for a longer-term horizon. During operation, however, fluctuations in transport requirements occur. Current systems cannot react flexibly and robustly, especially in the case of short-term, unexpected deviations of actual requirements from planned requirements. Overloading due to peaks in demand endangers the security of supply and must be absorbed by cost-intensive special transports. On the other hand, underutilization leads to an inefficient in-plant milkrun system.
The use of a dynamic control system, which flexibly takes into account the state of the system and the real transport requirements, should simultaneously increase the utilisation of the in-plant milkrun and reduce the resource requirements.
The algorithms to be developed determine routes, departure times and resource allocation (trains, employees, etc.) robustly at the optimal operating point at any time. This enables the system to operate stably even when transport requirements fluctuate at short notice. Overload cases and associated cost-intensive special transports are avoided. This requires the relocation of classic planning tasks, such as routing and scheduling, to the control system.
Typical application scenarios for in-plant milkrun systems will be used to show in which cases the use of dynamic control logic brings the greatest advantages.
Overall, it is assumed that dynamic resource allocation based on current transport requirements requires fewer resources than in existing, statically or semi-dynamically planned systems. In the case of medium- to long-term changes in transport requirements, there is no need to reschedule, apart from adjusting resources, as the control system automatically takes these changes into account.
Typical application scenarios for in-plant milkrun systems will be used to show in which cases the use of dynamic control logic brings the greatest advantages.
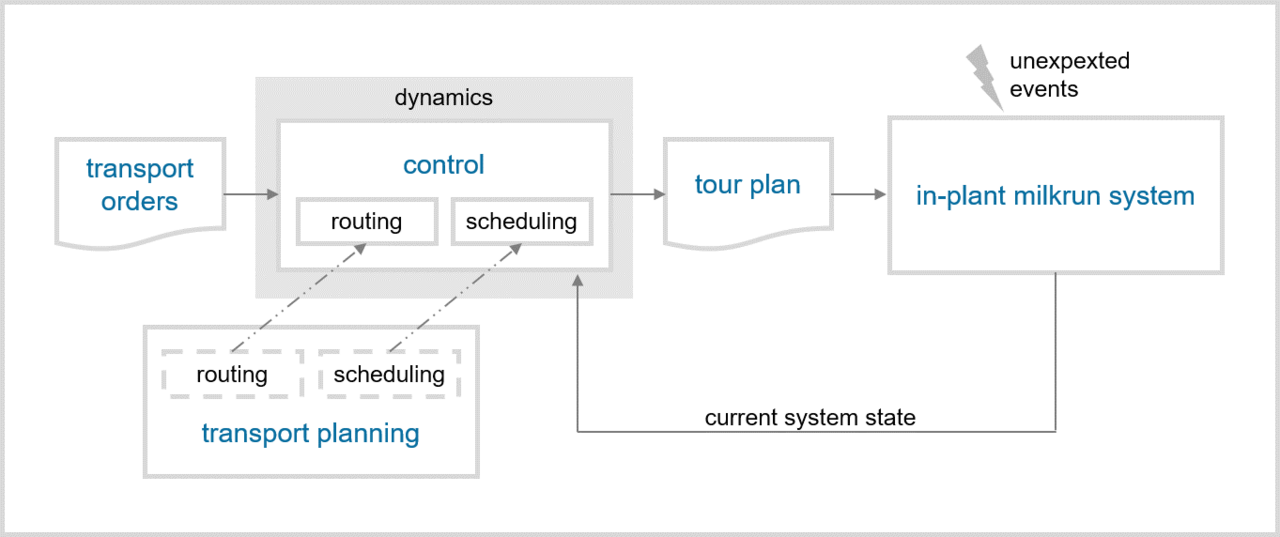
The research project will be carried out on the basis of six work packages.
In a first step, the components as well as the boundary conditions and input variables of a in-plant milkrun system are described and parameterised. In addition, the interactions between the system components will be analysed and typical deployment scenarios identified.
Overlapping objectives are defined as a basis for the evaluation of the concept in AP2 for route train control and its operationalisation by means of suitable key figures. Based on the description from AP1, the in-plant milkrun system (AP3) is modeled. System components, boundary conditions and input variables are converted into a generic model. In addition, the typical deployment scenarios of in-plant milkrun systems as well as a static reference system for the evaluation are mapped.
With the conception of the dynamic control algorithms AP4 represents the core of the project. Depending on the deployment scenario, the logics must continuously determine for each transport order which resource is to be used, on which route and on which tour, and at what time. Among other things, the times at which information is transferred to the in-plant milkrun system by the controller are defined. This provides a statement as to when current information can be taken into account by the controller.
AP5 comprises the implementation of the generic in-plant milkrun model as well as the control algorithms in a common computer model. Using discrete event simulation in the Tecnomatix Plant Simulation software, all models are verified and evaluated for each deployment scenario.
From the results of the systematic simulation experiments, AP6 finally derives which control logic is most suitable for which application with regard to the defined target values. Cases are also conceivable in which the best results can be achieved by applying static control.