P4: Gezielte umformtechnische Erzeugung von Eigenspannungen durch lokales Einprägen von Strukturen in Blechdickenrichtung zur Verbesserung der Bauteileigenschaften
Das Ziel des Projektes ist der Nachweis, dass durch die Kombination eines Tiefzieh- und Prägeprozesses gezielt Eigenspannungen in einem dünnwandigen Blechbauteil aus einem hochfesten, korrosionsbeständigen Stahl erzeugt werden können, um die Bauteileigenschaften nachhaltig positiv zu beeinflussen. Das Forschungsvorhaben wird als Kooperationsprojekt zwischen dem IFU Stuttgart (Institut für Umformtechnik), dem IAM-WK (Institut für angewandte Materialien) und dem ITM-KM (Institut für Technische Mechanik, Teilinstitut Kontinuumsmechanik) des Karlsruher Instituts für Technologie (KIT) durchgeführt, um die Fachexpertisen in den Bereichen Umform- und Werkstofftechnik sowie Mechanik in einem Projekt zu bündeln. Durch die Untersuchung einphasiger und grob mehrphasiger korrosionsbeständiger Stähle wird der Beitrag der phasenspezifischen Mikro-eigenspannungen systematisch bewertet
Ergebnisse der 1. und 2. Projektphase
Anhand vereinfachter Blechbauteilgeometrien wurde ein kombinierter Umform-, Präge- und Reformierprozess zum Einbringen eines homogenen ES-Zustands entwickelt und in einem prototypischen Realwerkzeug umgesetzt. Der Prozess wurde zunächst an einem ferritischen Edelstahl angewandt und anschließend auf den deutlich komplexeren Duplex-Edelstahl X2CrNiN23-4 übertragen.
Parallel dazu wurde der Ausgangsmaterialzustand umfassend charakterisiert. Das Blechmaterial weist typische Walztexturen in Austenit- und Ferritphase mit einem leichten Gradienten der Texturschärfe über die Blechdicke auf. Da die kristallographische Textur bei der simulativen ES-Bestimmung unbedingt zu berücksichtigen ist, wurde das richtungsabhängige elastisch-plastische Materialverhalten sowohl makroskopisch als auch auf phasenspezifischer Ebene analysiert. Im Hinblick auf die ES-Analytik wurden aufwändige einachsige Beanspruchungsversuche im Labormaßstab und am Deutschen Elektronen-Synchrotron DESY durchgeführt, auf dessen Basis eine verbesserte Auswertemethodik für den texturierten, grob zweiphasigen Duplexstahl erarbeitet werden soll. Die aus diesen experimentellen Versuchen gewonnenen Daten konnten als Input für ein zwei-skaliges Simulationsmodell verwendet werden, mithilfe dessen die Ausbildung phasenspezifischer ES auf allen Größenskalen unter Berücksichtigung der kristallographischen Textur und plastischen Anisotropie vorhergesagt werden konnte.
Der Abgleich der Simulation erfolgte am Beispiel eines tiefgezogenen Rundnapfes, sowie an einem 4-Punkt Biegeversuch. Die Simulationsergebnisse wurden anhand lokal bestimmter Verteilungen der Makro-ES (inkrementelle Bohrlochmethode) und phasenspezifischer ES (Röntgenbeugung) experimentell validiert.
Mittels zyklischer Belastungsversuche der gefertigten Blechproben wurde abschließend die Stabilität der ES und die Verbesserung der zyklischen Beanspruchbarkeit gezeigt.
Ziele der 3. Projektphase
Das übergeordnete Ziel in der FÖP III besteht darin, die in den bisherigen zwei FÖP erarbeiteten Erkenntnisse im Hinblick auf die Erzeugung, die Analyse, die Stabilität und die Simulation von ES auf ein zyklisch beanspruchtes Realbauteil, im Speziellen auf ein Trägerblech zu projizieren. Neben der Übertragung der erarbeiteten Methoden zu Prozessauslegung, ES-Simulation und ES-Analyse auf das Zielbauteil wird der Berücksichtigung der Texturentwicklung eine zentrale Bedeutung in FÖP III zugeordnet.
Das Arbeitsprogramm der FÖP III umfasst
-
die numerische Auslegung des Umformprozesses und Ableitung des Werkzeugkonzeptes
-
die experimentelle Analyse der Eigenspannungen auf allen Größenskalen (I. bis III. Art.)
-
die numerische Abbildung der lokalen Eigenspannungsentwicklung mittels mikromechanischer Ansätze ebenfalls auf allen drei Größenskalen und
-
die Untersuchung der ES-Stabilität und der zyklischen mechanischen Beanspruchbarkeit
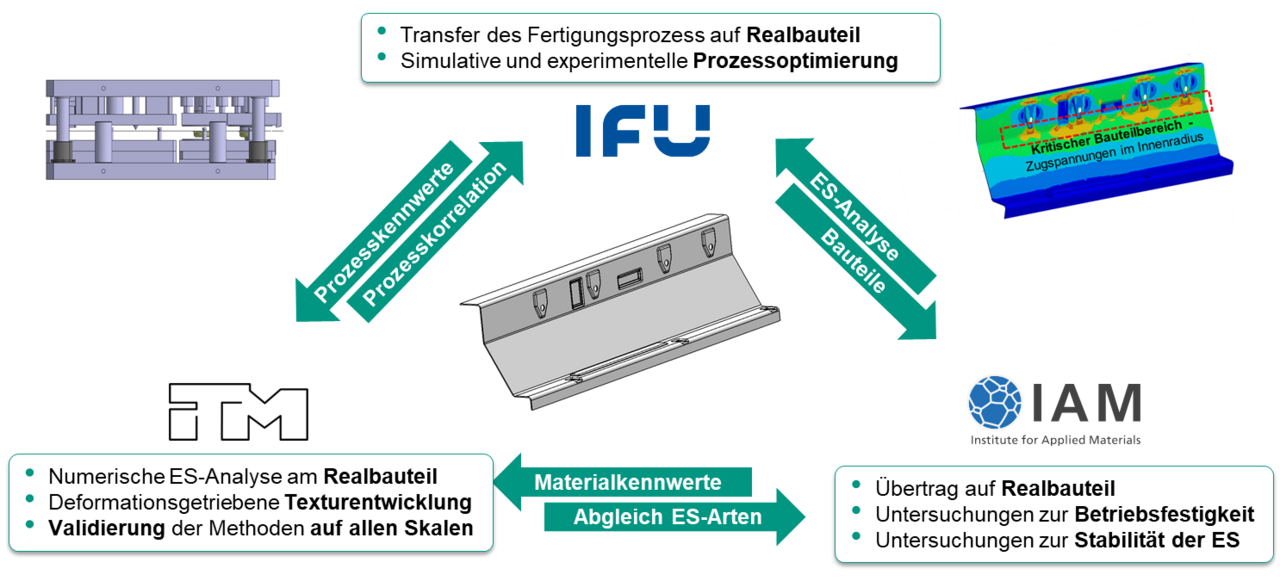
Ansprechpartner
Institut für Angewandte Materialien - KIT Karlsruher Institut für Technologie
Projektleitung P4.B
Dr.-Ing. Jens Gibmeier
Projektbearbeiter
Nicola Simon
Bereich für Kontinuumsmechanik - KIT Karlsruher Institut für Technologie
Projektleitung P4.A
Prof. Dr.-Ing. Thomas Böhlke
Projektbearbeiter
Maximilian Krause
Institut für Umformtechnik (IFU) - Universität Stuttgart
Projektleitung P4.C
Prof. Dr.-Ing. Mathias Liewald, Dr.-Ing. Kim Rouven Riedmüller
Projektbearbeiter
Pascal Heinzelmann
Veröffentlichungen
Übersicht über alle Veröffentlichungen aus dem SPP2013