Extrusion of Near-Nozzle Mixed Concrete –Individually Graded in Density and in Rate of 3D Fibre Reinforcement
Development, construction and validation of a continuous mixing system
Additive manufacturing in the construction industry represents one of the biggest changes in the last 50 years. On the one hand, the focus is on increasing efficiency in terms of required production time, as well as increasing resource efficiency. In contrast to filled concrete formwork castings, 3D concrete printing enables the possibility of using material specifically where it is needed. In addition, the use of continuous systems makes it possible to produce different types of concrete by adjusting the mixing ratios. This makes it possible to control not only the amount of material but also the properties of the concrete at specific points.
In most concrete extrusion processes used today, the concrete is premixed and transported to the nozzle in relatively long hoses by a pump. The complicated cleaning is a problem when using such hoses, as steel fibres that may have been used can get stuck in the hose. In addition, the friction occurring in the hose has a negative effect on the concrete properties. Thus, the already high demands on the concrete can partly not be reached. Such requirements include slow curing during the pumping process, which is in contrast to relatively fast curing after the deposition. Since there is only one concrete mix in the pump and the system is discontinuous, the possibilities of graded concrete strands are difficult or impossible to realize.


The aim of subproject A03 (TRR 277) for the chair fml is to provide a (nozzle-near) mixing system that is capable of continuously grading the concrete properties during printing. In the second year, the system is to be mounted on a 6-axis robot, which is why lightweight construction and reliability are the main focus, in addition to general resource efficiency.
The development and design will be based on a theoretical validation by simulations and calculations and a practical validation by field tests using two prototypes.
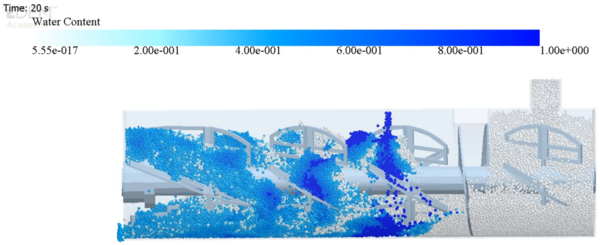
As a first step, a requirements analysis is carried out with the help of empirical values from field tests of a classical pump delivery from the Centre for Building Materials and Material Testing (cbm). Hereby a concept is developed which is elaborated to a virtual prototype by means of design calculations. This prototype is validated by DEM and FEM simulations before production. At this point, the theoretical calculations for the design are also revised in the course of an optimization using the input from the simulations.
After production, the mixing system is tested by field trials to reveal optimization potential. In the course of the conception, development and construction of a dynamic prototype V2 these potentials are to be incorporated. In further field tests V2 will be mounted on a Kuka 6-axis robot, tested and if necessary optimized in subsequent steps.
In addition to the design of the mixing system, its supply and discharge system and its control system will be developed.
The subproject A03 is funded by the Deutsche Forschungsgemeinschaft (German Research Foundation) (DFG-SFB TRR 277).