Durchsetzen hochfester Stähle
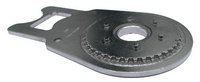
Die Reduzierung der Herstellkosten ist ein zentraler Faktor zur Erhöhung der Wettbewerbsfähigkeit produzierender Unternehmen. In diesem Kontext bietet das Durchsetzen große Potentiale, da es mit diesem Verfahren möglich ist, Funktionsflächen in nur einem Fertigungsschritt und ohne Nachbearbeitung zu erzeugen.
Das Durchsetzen ist in DIN 8587 als ein Schubumformverfahren, bei dem ein Werkstückteil gegenüber einem anderen mit einer geradlinigen Werkzeugbewegung verschoben wird, definiert. Die plastische Verformung wird, analog zum Feinschneiden oder Scherschneiden mit kleinem Schneidspalt, hauptsächlich durch einen Schubspannungszustand hervorgerufen. Ebenso ähneln sich die Werkzeugtechnik und Werkzeugkinematik der Verfahren. Dies lässt den Schluss zu, dass das Durchsetzen weitestgehend einem Schneidprozess ohne Durchschneiden des Werkstücks entspricht.
Zur Gewichtsreduktion von Bauteilen, sowie um auf einen Vergütungsprozess verzichten zu können, wird vermehrt auf Bleche aus hoch- und höchstfestem Stahl zurückgegriffen. In der Konstruktion und Entwicklung sind für diese Güten jedoch kaum Erfahrungswerte vorhanden. Um die Sicherheit des Prozesses bereits in der frühen Entwicklungsphase gewährleisten zu können, wird der Prozess mit der Finite-Elemente Methode simuliert. Hier ergeben sich besonders in der Materialmodellierung Herausforderungen.
Vom Scherschneiden ist bekannt, dass die Temperatur in der Scherzone auf über 300 °C steigen kann. Weiterhin sind Umformgrade und Dehnraten zu erwarten, die sich mit herkömmlichen Experimenten, wie dem Zugversuch, nicht abbilden lassen.
Ziel und Vorgehen
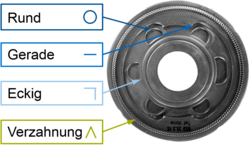
Das Ziel des Forschungsvorhabens war es, die Geometrie- und Machbarkeitsvorhersage von Blechbauteilen mit Durchsetzungen aus hoch- und höchstfesten Stählen zu verbessern. Hierzu wurde die Durchsetzlinie in wiederkehrende Formelemente zerlegt. Besonders relevante Formelemente wurden in einer Aufnahme des industriellen Ist-Zustandes ermittelt.
Diese geometrischen Elemente wurden anschließend in Experiment und Simulation untersucht und charakteristische Merkmale der Durchsetzungen ermittelt. Durch einen Optimierungsalgorithmus konnte die Abweichung zwischen gemessener und berechneter Kontur durch die Anpassung des Extrapolationsansatzes der Fließkurve minimiert werden. Die Machbarkeit für verschiedene Durchsetztiefen wurde durch Rissuntersuchungen besimmt.
Die so gewonnen Ergebnisse wurden anschließend in einer mit dem Simulationswerkzeug verknüpften Benutzeroberfläche gesammelt, um eine automatisierte Zuweisung der Materialeigenschaften zu nahezu beliebigen Durchsetzliniengeometrien zu erreichen. Dadurch konnte die Vorhersage ausgewählter Bauteileigenschaften und Prozessgrößen für das Durchsetzen hochfester Stähle erreicht werden.
Untersuchte Versuchsparameter
Für die Untersuchungen wurden die vier Blechwerkstoffe HSM 355, HLB 22, HSM 700 HD und Strenx 700 MC plus verwendet. Als Aktivelementwerkstoffe kamen K490 microclean und K110 zum Einsatz. Zur Abbildung der ausgewählten Formelemente wurden insgesamt fünf verschiedene Geometrien untersucht. Eine zusätzliche Geometrie diente der Validierung der Ergebnisse. Weiterhin wurden die Stößelgeschwindigkeit, die Durchsetztiefe und der Zustand der Aktivelemente (beschichtet/unbeschichtet) untersucht. Der Durchsetzspalt wurde konstant zu -25 µm gewählt.
Experimentelle Ergebnisse

In den Durchsetzexperimenten, welche auf einer Feinschneidpresse des Typs "HFA 3200 plus" der Firma Feintool Technologie AG, Lyss (Schweiz), durchgeführt wurden, konnte ein stark unterschiedliches Verhalten der zwischen HSM 355 und HLB 22 sowie HSM 700 HD und Strenx 700 MC plus beobachtet werden. Dies äußerte sich besonders an den nötigen Kräften sowie dem Kanteneinzug und dessen Geomtrieabhängigkeit.
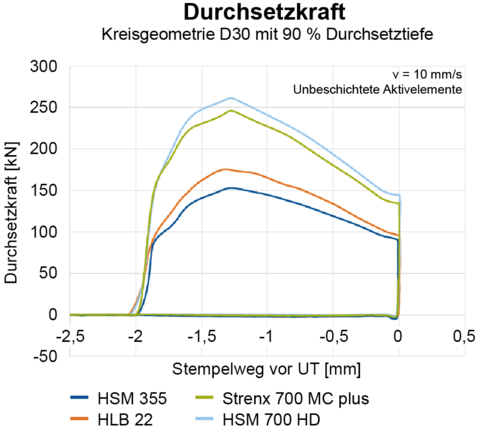
So konnte für HSM 700 HD und Strenx 700 MC plus eine in etwa 70 % höhere Durchsetzkraft wie bei HSM 355 und HLB 22 bei sonst ähnlichem Kraftverlauf beobachtet werden. Weiterhin wurde eine Geometrieabhängigkeit der spezifischen Durchsetzkraft beobachtet.
Erhebliche Unterschiede konnten auch beim Kanteneinzug gemessen werden. So wiesen die beiden hochfesten Werkstoffe beim Durchsetzen einer Kettengliedgeometrie an einer konvexen Messstelle einen um 40 % niedrigeren Kanteneinzug auf als die Referenzwerkstoffe. Dieser Effekt kehrt sich bei konkaven Messstellen jedoch um, wo bei den Blechwerkstoffen mit niedrigerer Streckgrenze ein um
20 % reduzierter Kanteneinzug festgestellt werden konnte.
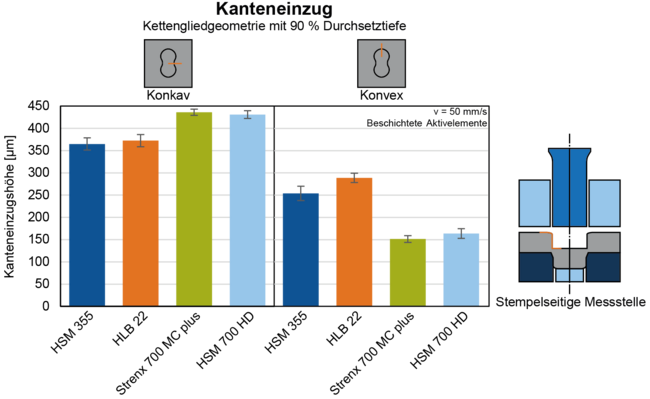
Simulationsgestützte Ergebnisse

Es wurden sechs Simulationsmodelle aufgebaut die eine Abbildung des Durchsetzprozesses unter den zu variierenden Prozessparametern erlauben. Durch einen im Projekt erarbeiteten Optimierungsalgorithmus konnte die Abweichung zwischen Simulation und Experiment durch formelementspezifische Korrekturfaktoren des Materialmodells minimiert werden.
Durchsetzsimulationstool (DurST)
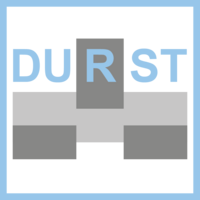
Im Rahmen des Projektes wurde ein Programm entwickelt, das die automatisierte Erstellung von Durchsetzsimulationen mithilfe einer Benutzeroberfläche erlaubt. Die aktuelle Version der Oberfläche kann unter folgendem Link heruntergeladen werden:
DurST_v1.0 (ausführbare .exe-Datei)
Der Quellcode kann auf Anfrage zugesandt werden.
Kontakt: jens.stahl@utg.de
Durch die Implementierung mit quellenoffener Software ist eine Erweiterbarkeit der zugrundeliegenden Datenbank gewährleistet. Weiterhin kann mithilfe der integrierten Durchsetzkraft- und Machbarkeitsabschätzung eine Beurteilung eines Blechbauteils mit Durchsetzungen schon in der frühen Entwicklungsphase erfolgen.
Förderhinweis
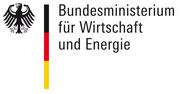
Förderhinweis Das IGF-Vorhaben „Machbarkeits- und Geometrievorhersage von Blechbauteilen mit Durchsetzungen aus hoch- und höchstfesten Stählen“, IGF-Projekt Nr. 18625 N, der Forschungsvereinigung Stahlanwendung e. V. (FOSTA), Sohnstraße 65, 40237 Düsseldorf wurde über die AiF im Rahmen des Programms zur Förderung der industriellen Gemeinschaftsforschung (IGF) vom Bundesministerium für Wirtschaft und Energie aufgrund eines Beschlusses des Deutschen Bundestages gefördert.