Reproduktion und Modifikation eines chemisch resistenten Piezomembrandruckkopfes
Theoretische / Experimentelle Semesterarbeit betreut durch Markus Kagerer und Tim Lüth.
Problemstellung
Ein Forschungsgebiet des Lehrstuhls für Mikrotechnik und Medizingerätetechnik stellen Piezomembrandruckköpfe dar. Auf einen strukturierten Siliziumwafer, der die fluidischen Komponenten, wie Fluidzuführung, Pumpkammer und Düse enthält, wird eine Membran aus Borsilikatglas gebondet. Hierauf wiederum wird der Aktor, der aus strukturierten Piezozungen besteht, aufgebracht. Bislang wird das zu druckende Fluid über eine Spritze dem Druckkopf zugeführt. Dies ermöglicht für spätere Anwendungen kein autonomes Arbeiten. Des Weiteren fehlt die Möglichkeit, Stoffe, die einen Phasenübergang vom festen in den flüssigen Zustand vollziehen, zu drucken. Dies ist insbesondere beim Mikro 3D-Druck essentiell, bei dem es gilt, Stoffe wie Polymere oder Wachse zu drucken. Bislang werden die einzelnen Bestandteile des Druckkopfes mit der Lasermikrobearbeitung erstellt. Dies bedeutet einen Ebenenabtrag der Pumpkammer, der Düse und der Fluidzuführung im Siliziumwafer. Die Seitenwände sind durch den großen Spotdurchmesser von ~ 50 µm bei dem verwendeten IR Laser LS2000 rau. Aufgrund von Vielfachreflexionen des Laserstrahls an den Seitenwänden in der Bearbeitungsfuge, verjüngt sich die Form zudem nach unten. Insbesondere die Düsenform stellt für die Tropfenbildung einen wichtigen Parameter dar. Senkrecht glatte Düsenformen würden weniger Reibung in der Düse bedeuten, so dass der Aktor weniger Energie für den Tropfenausstoß liefern muss. Zudem würde die Bildung von Satellitentropfen reduziert werden. Des Weiteren werden die Piezozungen und die passive Membran aus Borsilikatglas durch den Laser hergestellt. Borsilikatglas absorbiert nur bei kleinen Wellenlängen die Energie des Laserstrahls. Das hierzu am Lehrstuhl zur Verfügung stehende UV Lasersystem ist mit 2 W mittlerer Leistung leistungsschwach, so dass im Ergebnis die Herstellung der Membran bis zu 30 min dauert und nur eine zeitintensive Batchherstellung hiermit ermöglicht wird. Gleiches gilt für die Strukturierung der Piezozungen. Es treten zudem Leistungsschwankungen bei dem zu verwendenden IR Laser auf, so dass es nicht möglich ist, die Pumpkammer über den gesamten Herstellungsprozess gleich tief zu erstellen.
Stand der Technik
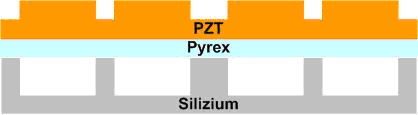
Der Tropfenerzeuger besteht aus einem 525 µm Siliziumwafer, einer 250 µm Borsilikatglasmembran und einem Piezoaktor. Hierbei bildet die Membran die Wand zu einer Kammer in der Siliziumgrundplatte, die mit dem Fluid gefüllt ist (siehe Abbildung 1).
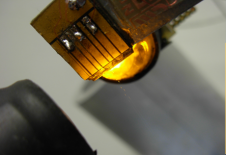
Die Deformation des Piezoaktors, welcher sich auf der Membran befindet, ändert das Volumen der Kammer; hierdurch wird der Tropfenausstoß aus der 50-200 µm breiten Düse initiiert. Die Dicke des Piezoaktors kann je nach Verwendungszweck variiert werden. Es können sowohl Einzel- als auch Mehrdüsensysteme aufgebaut werden (siehe Abbildung 2). Je nach verwendeter Piezokeramik liegt die mögliche Einsatztemperatur bei bis zu 250 °C. Dabei wird der Aktor, je nach Trennbreite der Elektroden und Dicke der Keramik, mit bis zu 150 V angesteuert. Es kann ein Tropfenvolumen zwischen 40-1500 pl je nach Dimensionierung des Druckkopfes erreicht werden. Über die Variation der Ansteuerparameter werden Fluggeschwindigkeiten der Tropfen von 1 m/s bis zu 10 m/s erreicht. Die Grenzfrequenz liegt abhängig von der Konstruktion bei über 10 kHz.
Kritik am Stand der Technik
Bislang ist es nicht möglich, die Herstellung der Piezomembrandruckköpfe im Batch durchzuführen, so dass sich ein hoher Zeitaufwand bei deren Herstellung ergibt.
Durch die Herstellung der Düse mit dem Laser erfolgt eine Verjüngung ihrer Form nach unten. Hierdurch wird die Bildung von Satellitentropfen verstärkt. Durch den relativ großen Spotdurchmesser des IR Lasers sind die Seitenwände im Düsenkanal rau, so dass der Piezoaktor einen größeren Energieeintrag liefern muss, um die damit verbundene Reibung zu überwinden. Durch die vorherrschenden Leistungsschwankungen des IR Lasers ist es bislang nicht möglich, die Tiefe der Pumpkammer reproduzierbar zu erstellen.
Da bislang kein Fluidreservoir mit integrierter Heizwicklung am Druckkopf montiert ist, besteht keine Möglichkeit feste Stoffe mit Phasenübergang zu drucken. Dies würde im Mikro 3D-Druck neue Perspektiven ermöglichen.
Aufgabenstellung
Der Tropfenerzeuger ist ein Sandwichaufbau, bestehend aus einem 525 µm Siliziumwafer, einer 250 µm Borsilikatglasmembran und einem strukturierten Piezoaktor. Hierbei bildet die Membran die Wand zu der Kammer in der Siliziumgrundplatte, die mit dem Fluid gefüllt ist.
Da die Leistung des IR Lasers LS2000 Schwankungen unterliegt, gilt es eine Prüfmethode zu entwickeln, mit der es möglich ist, exakt die Pumpkammertiefe im Siliziumwafer abhängig von der aktuellen Leistung zu erstellen.
Sowohl die Strukturierung der Elektroden, das Freilegen der Düse als auch die Erstellung der passiven Membran aus Borsilikatglas sollen anstatt bisher mit dem Laser zukünftig mit der Wafersäge DISCO DAD 321 vorgenommen werden. Dies erlaubt einen wesentlich schnelleren Arbeitszyklus, zudem ergibt sich die Möglichkeit zur Batchherstellung. Hierbei gilt es, die Wafersäge exakt zu positionieren, das Schneidprogramm zu erstellen und die richtigen Sägeblätter zu wählen.
Damit der Druckkopf zukünftig autonom arbeitet und auch das Drucken von festen Fluiden ermöglicht wird, gilt es ein Fluidreservoir mit integrierter Heizwicklung zu erstellen. Hierbei soll eine Temperatur von bis zu 200 °C im Inneren des Tanks erreicht werden. Hierbei muss auf die Curietemperatur der verwendeten Piezokeramik geachtet werden, damit diese nicht depolarisiert wird (PIC151 ~ 250 °C).
Die Validierung des modifizierten Druckkopfes erfolgt anhand von Experimenten, in denen es gilt, Fluide zu drucken, die einen Aggregatsübergang aus der festen in die flüssige Phase vollziehen. Hierbei sei an handelsübliches Kerzenwachs oder Polypropylene im ersten Schritt zu denken.
Im Rahmen dieser Arbeit soll sowohl die reproduzierbare Herstellung der Piezomembrandruckköpfe ermöglicht werden als auch deren Modifizierung erfolgen. Für die Herstellung und Charakterisierung der Piezomembrandruckköpfe stehen gängige Mikrotechnik-Tools zur Verfügung. Für den Aufbau und die Inbetriebnahme bietet der Lehrstuhl eine umfangreiche Laborausstattung sowie eine eigene Werkstatt.
Erwartete Vorteile und Funktionen der Lösung
Bisher aufgebaute Piezomembrandruckköpfe zeichnen sich durch eine konische Form der Düse und rauen Seitenwände aus. Durch die Herstellung der Düse mit der Wafersäge wird es möglich, die Reibung im Kanal zu minimieren und den benötigten Energieeintrag des Aktors zu reduzieren. Die bislang entstehenden Satellitentropfen werden zudem durch die senkrechten Wände minimiert und der Tropfenbildungsprozess wird in eine reproduzierende Weise überführt. Durch die Integration der Wafersäge in den Herstellungsprozess wird die Batchherstellung deutlich gesteigert und die Herstellungszeit minimiert. Das Anbringen eines Fluidreservoirs mit integrierter Heizwicklung wird es zukünftig ermöglichen, Stoffe, die einen Phasenübergang vom festen in den flüssigen Zustand ermöglichen, zu drucken. Die Möglichkeit des Druckens von festen Fluiden in der Mikrotechnik eröffnet neue Möglichkeiten für das gesamte Rapid Prototyping. Insbesondere für den 3D-Druck ist dies aus Gesundheitsaspekten eine wichtige Alternative zu chemischen Reaktionen. Bspw. können Polymere verarbeitet werden. Diese Stoffgruppe zeichnet sich durch ein hohes Anwendungspotential aus, da verschiedene Eigenschaftsspektren erzielbar sind. Epoxidharze weisen hohe Festigkeiten bei hohen E-Moduli auf. Polyurethane sind mit Hilfe ihrer Komponenten von fest bis elastisch einstellbar. Die Anwendungen liegen hierbei im 3D-Druck oder auch bei Spezialbeschichtungen. Zum Teil wären aus chemischer Sicht niederviskose Alternativen vorhanden, die aber aus Gesundheitsaspekten oft nicht zum Einsatz kommen können.
Realisierung und Ergebnisse
Erwartung:
Für die Bearbeitung der genannten Aufgabe wird folgendes erwartet:
- Ausführliche Dokumentation der einzelnen Schritte.
- Strukturiertes Vorgehen, d.h. zuerst eine Problembeschreibung erstellen und dann Lösungsansätze vergleichen.
- Beschreibung der Lösungsstruktur und Abgrenzung gegenüber anderen Lösungen.
- Experimente zur Bestätigung der gefundenen Lösung.
Wird ein Ziel nicht erreicht, dann soll dieser Umstand ausreichend begründet werden. Das Erreichen bzw. Nichterreichen des Ziels soll untersucht und dokumentiert werden, so dass fundierte Aussagen über die Eignung oder über eine notwendige Änderung gemacht werden können.
Vorgehen:
1. Recherche des Stands der Technik im Bereich der Laserablation, der Drop-on-demand Drucktechnik und der Reservoirintegration.
2. Gegenüberstellung und Bewertung der vorgeschlagenen Lösungsansätze.
3. Konstruktion eines Fluidreservoirs mit integrierter Heizung.
4. Reproduzierbare Herstellung der Piezomembran-druckköpfe.
5. Experimente zum Nachweis des Druckens von festen Fluiden.
6. Anfertigung der schriftlichen Ausarbeitung.
Ergebnisse:
- Reproduzierbare Herstellung des Piezomembran-druckkopfes im Batch.
- Integration eines Fluidreservoirs mit integrierter Heizung.
- Konstruktionszeichnungen des gefertigten Fluidreservoirs.
- Dokumentierte Versuche.
- Anfertigung der Semesterarbeit.
Publikationsmöglichkeiten
- Vergleich des Tropfenbildungsprozesses zwischen senkrecht glatter und konisch rauer Düse.
- Gegenüberstellung des geforderten Energieeintrages des Aktors zwischen senkrecht glatter und konisch rauer Düse.
- Aufzeigen einer kostengünstigen Experimentierplattform, die zudem in kurzer Zeit hergestellt werden kann. Es können fluidische dimensionslose Kennzahlen, wie Weber-, Reynolds- oder auch Ohnesorge Zahl schnell in die Dimensionierung der Druckköpfe miteinbezogen werden.
Referenzen
Irlinger, F.; Günther, D.; Scheuenpflug, M.; Lüth, T.C. (2007): Von der Idee zum Mikrofluidsystem. Mikrosystemtechnik, Chemnitz, 14.-15.11.2007. In Dötzel, Müller (Ed.), 8. Chemnitzer Fachtagung Mikromechanik & Mikrotechnik, TU Chemnitz, pp. 11-15.
Heinzl, J., Harnisch, J., Irlinger, F., Hoffmann, H., Petry, R., Stanchev, S., et al. Technologien für die Fertigung individualisierter Produkte. In U. Lindemann, R. Reichwald, & M. F. Zäh, (Eds.), Individualisierte Produkte - Komplexität beherrschen in Entwicklung und Produktion. (pp. 89-113). Springer-Verlag, Berlin, Heidelberg.
W. R. Wehl, "Ink-jet printing: the present state of the art," in Proc. IEEE CompEuro '89 Conf. VLSI and Computer Peripherals, Washington, pp. 46-52.
H. Wijshoff, "The dynamics of the piezo inkjet printhead operation," Physics Reports, vol. 491, no. 4-5, June 2010, pp. 77-177.
J. Heinzl, "Ink Jets," in Comprehensive Microsystems, 1st ed. G. Yogesh, T. Osamu, and Z. Hans, Ed., Oxford: Elsevier, 2008, pp. 335-368.