Manufacturer | HBM, Kyowa |
Model | diverse |
Brief Description:
The strain gauge is a widely used measurement technique with a large and diverse range of applications to detect strain. Strain gauges have very high accuracy and can measure even the smallest strains. The strain gauges' working principle bases on the "Thomson effect." This effect describes the proportional change of the electrical resistance to the strain. The strain gauge contains a measuring grid (e.g., constantan foil), which lies between the measuring grid carrier and the cover layer (both made of, e.g., polyamide). The strain gauge is applied to the respective material using a specially developed adhesive. During application, extreme cleanliness is necessary to achieve high measurement accuracy.
Main Areas of Application:
- High-precision measurement of the change in shape (strain)
- Determination of the initial modulus of elasticity
- Measurement of residual stresses (see borehole logging device)
Photo gallery:
Manufacturer | GOM GmbH (a ZEISS company) |
Model | Argus v6 3.0 |
Brief Description:
The Argus photogrammetric system from GOM finds use at utg. With this method, strain distributions resulting from the forming process can be objectively determined over large component areas and visualized in false color representations. Images of a marked component taken with a CCD camera can be processed using an integrated image evaluation system. The shape changes can be determined with an accuracy of about +- 0.5% (technical strain).
Technical Specifications:
Data Acquisition | Interface for the use of different types of cameras |
Calculation of the Deformation | Automatic Calculation of 3D Suface Coordinates |
Evaluation | Import of forming limit diagrams and visualization of measurement results |
Main Areas of Application:
- Determination of strain distributions of pre-strained specimens for the generation of bilinear strain paths
- Evaluation of strains in forming investigations
- Calculation of thinning and surface defects
- FEM comparison
Manufacturer | GOM GmbH (a ZEISS company) |
Model | Aramis SRX (adjustable) |
Brief Description:
The GOM Aramis SRX belongs to the "Digital Image Correlation" (DIC) measuring systems. During deformation, images of the component are recorded with two cameras. This recording allows the measurement of 3D displacements and strains on any object geometry. A random dot pattern is applied to the specimen for measurement. The image correlation algorithms work similar to pattern recognition methods and identify the displaced and deformed pattern in the recorded camera images. The measured pixel coordinates of the pattern, displacements, and strains in the component surface are computed for the area and with high precision.
Technical Specifications:
Camera Resolution | 4096 x 3068 Pixel |
Maximum Frame Rate | 75 Hz at full resolution 490 Hz at lower resolution (HD) |
Measuring Range | 30 x 22 mm2 … 245 x 185 mm2 |
Lighting | Light projector with blue light technology |
Usage | Flexible use on a tripod |
Main Areas of Application:
- Determination of characteristic values in the field of material characterization
- Determination of the edge crack sensitivity FEM comparison
Photo Gallery:
Manufacturer | GOM GmbH (a ZEISS Company) |
Model | Aramis 4M |
Brief Description:
The GOM Aramis 4M belongs to the "Digital Image Correlation" (DIC) measuring systems. During deformation, images of the component are recorded with two cameras. This recording allows 3D displacements and strains to be measured on any object geometry. A stochastic point pattern is applied to the specimen for measurement. Image correlation algorithms work similarly to pattern recognition methods and identify the displaced and deformed pattern in the recorded camera images. The measured pixel coordinates of the pattern, displacements, and strains in the component surface are computed over an area and with high precision.
Brief Description:
Camera Resolution | 2400 x 1728 pixel |
Maximum Frame Rate | 168 Hz at full resolution |
Measuring Range | 25 x 18 mm2 … 420 x 300 mm2 |
Lighting | 2 LED lights |
Strain Accuracy | Up to 0,01 % |
Main Areas of Application:
- Determination of characteristic values in the field of material characterization
- Permanently installed on the sheet of metal forming testing machine
Photo Gallery:
Manufacturer | ZwickRoell GmbH & Co. KG |
Model | LaserXtens Array 7-220 HP |
Brief Description:
The LaserXtens is a non-contact extensometer that performs tests with the highest precision without any measuring marks. It does not require any sample marking. The sample is illuminated with laser light, and the reflected laser beams generate a speckle pattern in the camera. This method is highly accurate and offers a wide range of evaluation options. Since no sample marking is required, it saves much time.
Technical Specifications:
Structure | 7 high-resolution digital cameras |
Accuracy Class | 0,5 according to EN ISO 9513 |
Visual Field | 220 mm x 28 mm |
Resolution | 0,07 μm |
Mwasuring Path with Speckle Tracking | 210 mm minus the initial measuring distance |
Initial Measuring Distance | 3 ... 200 mm |
Maximum Tracking Speed on the Specimen | 500 mm/min |
Measuring Frequency | 70 Hz (at default setting) |
Connection | Permanently installed on ZwickRoell AllRound Line Z150 |
Interface | ZwickRoell TestControl |
Evaluation | ZwickRoell TestXpert |
Main Areas of Application:
- Determination of characteristic values in the field of material characterization
- Strain measurement in tensile and compression tests
Photo Gallery:
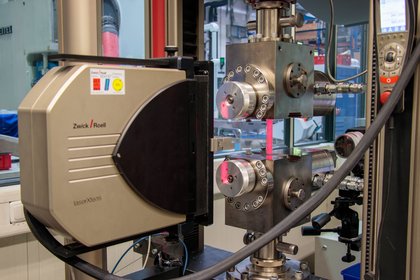
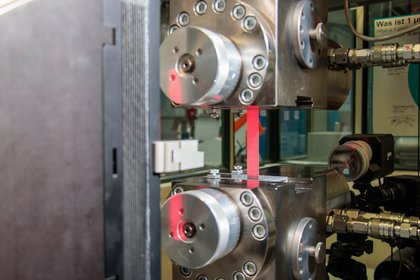
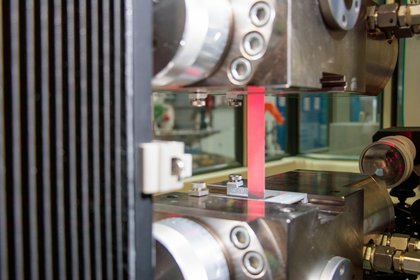
Hersteller | ZwickRoell GmbH & Co. KG |
Modell | Length: displacement transducer 066550; Width: displacement transducer 066792 |
Brief Description:
hese extensometers find a use for the direct length and width change measurement in tensile tests. They have an extensive, continuously adjustable measuring range that is set according to the tested specimen. Clip-on extensometers and extensometers with measuring probes are in direct mechanical contact with the specimen using measuring blades aligned perpendicularly to the measuring length.
Technical Specifications:
Measuring Range | 0,02 ... 50 mm (length change) |
Resolution | 0,1 µm (length and width change) |
Main Areas of Application:
- Determination of the mechanical parameters in the uniaxial tensile
Photo Gallery:
Manufacturer | MIOPAS |
Model | SPK-155 |
Brief Description:
Fiber Bragg gratings (FBG) are optical strain sensors in the core of a conventional single-mode optical glass fiber. The refractive index's periodic modulation makes the fiber strain sensitive along its longitudinal axis. The SPK-155 interrogator applies a broadband light spectrum in the infrared range to the FBG and measures the reflected light, which adds to a peak within the FBG due to positive interference. The peak position provides information about the strain state of the sensor. Due to the heat resistance of the glass fiber up to approximately 800°C and the resistance to liquid aluminum's corrosive effect, this measuring principle is suitable for determining strain during solidification and cooling of aluminum castings. Another application arises from the embedding of FBG in the inorganically bonded molding material. This aspect makes it possible to observe strains in cores during the casting process.
Technical Specifications:
Wavelength Range | 1510 ... 1595 nm |
Resolution | 0,1 pm |
Maximum Measuring Frequenzy | 15 kHz |
Maximum Optical Channels | 40 |
Maximum Channels with Multiplexing | 40 |
Interfaces | USB, Ethernet, analog |
Main Areas of Application:
Strain measurements in foundry operations using FBG:
- Strain measurement during solidification and cooling of casting materials
- Measurement of strain on inorganically bonded cores during casting
- Measurement of temperatures, vibrations, and pressures
Photo Gallery:
Manufacturer | SINT Technology s.r.l. |
Model | MTS3000 - Restan |
Year of Production | 2004 |
Brief Description:
The MTS3000 enables the automatic measurement of residual stresses on specimens up to 1 mm below the surface. According to the borehole method, the measurement is carried out as per ASTM standard E837. For this purpose, a hole is milled in the specimen in stages using a face mill. A strain measuring gauge rosette measures the strain changes in the area around the hole. The milling cutter is driven by a compressed air turbine, which allows a maximum speed of 400.000 rpm.
Technical Specifications:
Milling | The face of the milling cutter: coated with titanium nitride Nominal Diameter: 1,6 mm |
Maximum Depth | 1 mm |
Maximum Milling Cutter Rotation Speed | 400.000 rpm |
Main Areas of Application:
- Dertermination of residual stresses
Equipment:
- HBM Spider 8 amplifier for strain measurment via strain gauge
- Ocular camera for checking the milled hole
Photo Gallery:
Manufacturer | IDT |
Model | Os3-S2 |
Brief Description:
The IDT Os3-S2 is a new high-speed digital camera designed to operate in the most demanding environments. The Os-3's most prominent design feature is its compact size combined with a wide data bus, allowing it to achieve very high frame rates, including transfer speeds to a (non-volatile) high capacity solid-state memory.
Technical Specifications:
DDR Memory | 16 GB |
Admission Rate | 5.000 Hz (at 1280 px. x 1024 px.) 152.000 Hz (at 320 px. x 640 px.) |
Color Depth | 12 bit |
Main Areas of Application:
- High-speed testing
- Inverse material characterization
- Material testing