Manufacturer | Schuler GmbH |
Model | CSC 1000 |
Year of Production | 2015 |
Brief Description:
The Schuler GmbH, Göppingen, CSC 1000 servo press in the C-frame design is used for blanking and forming operations on small parts. The individual adjustment of the stroke height using the reversing movement (pendulum stroke) of a torque motor allows for flexible use of the press. Individual adjustment of the slide kinematics to the process parameters allows an adaption of the press to the forming process. The press operation mode is either manual or automatic.
Technical Specification:
Nominal Press Force | 1000 kN |
Maximum Strokes in a Countinous Stroke (Pendulum Stroke) | 130 strokes/min |
Machine-Bed Dimensions | 950 mm x 660 mm |
Main Areas of Application:
- Investigation on the influence of different process parameters on component quality and tool wear in shear cutting and forming processes
- Continous stroke tests during shear cutting
Equipment:
- EV 132 TM electronic roll feed unit from Zehnder & Sommer GmbH, Witten
- Required drive torque provided via servomotor
- cooling unit for cooling the drive motor
- brake unit for generating the hydraulic energy, for operating the holding brake
Photo Gallery:
Manufacturer | Dieffenbacher GmbH |
Model | DXU 320 B |
Year of Production | 1996 |
Brief Description:
The Dieffenbacher double-acting hydraulic top ram press is used to punch and for the active and passive drawing of sheet metal. The forty-ton system has a nominal pressing force of 3500 kN and a drawing cushion force of 1250 kN and is therefore also suitable for large forming processes. Due to the accessibility from both sides in the column design, the press can be used very flexibly for a wide range of applications and unique processes.
Technical Specification:
Nominal Press Force | 3500 kN |
Draw Cushion Force | 1250 kN |
Maximum Drawing Speed | 30 mm/s |
Clamping Plate Area | 1600 x 1300 mm |
Maximum Tool Height | 900 mm |
Main Areas of Application:
- Generation of pre-strains in sheets for material testing
- Forming operations for material testing
- Unique processes (e.g.. ECAP or bead embossing)
- Collar forming
Equipment:
- Large Marciniak tool with various inserts
- Equal-channel angular pressing (ECAP) for sheet materials
- Cross-die tool for material validation
- Collar pulling tool
- hotset© cartridge heater control unit for mold temperature control
-
Measurement technology for the investigation of pressing forces
Photo Gallery:
Manufacturer | Feintool International Holding AG |
Model | HFA 3200 Plus |
Brief Description:
The fine blanking press, type HFA 3200plus from Feintool, has a total press force of 3200 kN. This pressing force consists of the cutting, ring-jaw, blank holder, and counter holder forces. The welded design of the press body's monobloc as well as the large column cross-sections and additional ribbing of the press, guarantee a high press rigidity. In combination with the slide's guide accuracy, this press enables the production of precision components with a high degree of dimensional accuracy, whose cut surfaces have the character of functional surfaces without post-processing. Sheet thicknesses of up to 16 mm can be processed.
Technical Description:
Maximum Total Press Force | 3200 kN |
Maximum Plunger Stroke | 180 mm |
Stroke Rate | 85 strokes/min |
Maximum Ring Force | 1400 kN |
Maximum Counterholder Force | 700 kN |
Cutting Speed | 5 ... 70 mm/s |
Clamping Area | 630 x 630 mm |
Main Area of Application:
-
Investigations in the field of cold forming, normal and fine blanking processes
Equipment:
- Various tools for creating different geometrics
- A unique tool for measuring the temperature at the punch cutting edge
- Belt oiling system
- Oil mist extraction system
Photo Gallery:
Manufacturer | Bruderer AG |
Model | BSTA 510-125 |
Year of Production | 2019 |
Brief Description:
High-performance punching machine with complete mass balancing and adjustment stroke. Precise mechanics with universal application possibilities for the most diverse tasks and an optimal cost-benefit ratio.
Technical Specifications:
Nominal Force | 510 kN |
Stroke Rate | 50 ... 1050 strike/min |
Lifting Height | 16 ... 51 mm |
Mold Installation Height | 263 ... 344 mm |
Cutting Speed | 5 ... 70 mm/s |
Clamping Plate Area | 1240 mm x 650 mm |
Main Areas of Application:
- Wear tests in single and continuous operation to increase tool life
-
Investigation of process-related influencing variables of forming and cutting tests
Equipment:
- BSV 170 servo roll feeder
- Adjustable stroke with mass compensation
- Thermoneutral ram guide with tilting point in the direction of the belt
- Integrated measuring and monitoring function
-
Ram adjustment during the run under production conditions
Photo Gallery:
Manufacturer | Bruderer AG |
Model | BSTA 1600-181 |
Year of Production | 2018 |
Brief Description:
High-performance punching machine with complete mass balancing and adjustment stroke. Precise mechanics with universal application possibilities for the most diverse tasks and an optimal cost-benefit ratio.
Technical Specification:
Nominal Force | 1600 kN |
Stroke Rate | 100 ... 800 stroke/min |
Lifting Height | 19 ... 100 mm |
Mold Installation Height | 345 ... 475 mm |
Clamping Plate Area | 1790 mm x 1070 mm |
Main Areas of Application:
- Wear tests in single and continous operation to increase tool life
- Investigation of process-related influencing variables of forming and cutting tests
Equipment:
- BSV 300 servo roll feeder
- Adjustable stroke with mass compensation
- Thermoneutral ram guide with tilting point in the direction of the belt
- Integrated measuring and monitoring function
- Ram adjustment during the run under production condition
Photo Gallery:
Manufacturer | SYS |
Model | SHP-400 |
Year of Production | 2014 |
Brief Description:
The servo stroke press is used at utg to generate forces on test benches due to its high flexibility. Its bottom center point has excellent accuracy, even when off-center forces are applied. It also has a high level of slide parallelism due to the preloaded roller guides. The nominal pressing force is available over the entire stroke. The stroke is infinitely adjustable.
Technical Specification:
Dynamic Nominal Force | 400 kN |
Stroke Rate | 5...300 stroke/min |
Lifting Height | 0 ... 100 mm |
Mold Installation Height | 280...380 mm |
Clamping Plate Area | 1070 mm x 800 mm |
Main Areas of Application:
- Dynamic testing on in-house developed test benches
- Single stroke shear cutting tests
Equipment:
- High-speed camera
Photo Gallery:
Manufacturer | Otto Bihler Maschinenfabrik GmbH & Co. KG |
Model | GRM-NC |
Brief Description:
The GRM-NC automatic punching and bending machine has a modular design and essentially consists of a gripper feed, a 400 kN servo press and eight independently controllable servo axes - six arranged radially, two in the depth direction - each with a nominal force of 31 kN. The six radially arranged servo units can be freely positioned within their working range, and the adjustment of the units is automated. In combination with Bihler's standardized LEANTOOL modular tool system, the system and the tool can thus be flexibly and quickly adapted to a wide range of applications.
Technical Specifications:
Stroke Rate | 0 ... 240 stroke/min |
Maximum Nominal Press Force of the Two-Point Eccentric Press | 400 kN |
Nominal Press Force of each Servo Unit | 31 kN |
Main Areas of Application:
- Manufacture of stamping and bent components
- Research on the rebound behaviour of stamped and bent components
- Investigation on the avoidance of slug pulling
Equipment:
- HSB-tool (for research on slug pulling)
- Optibend tool (for rebound research)
- Stamp fatigue test bench
Photo Gallery:
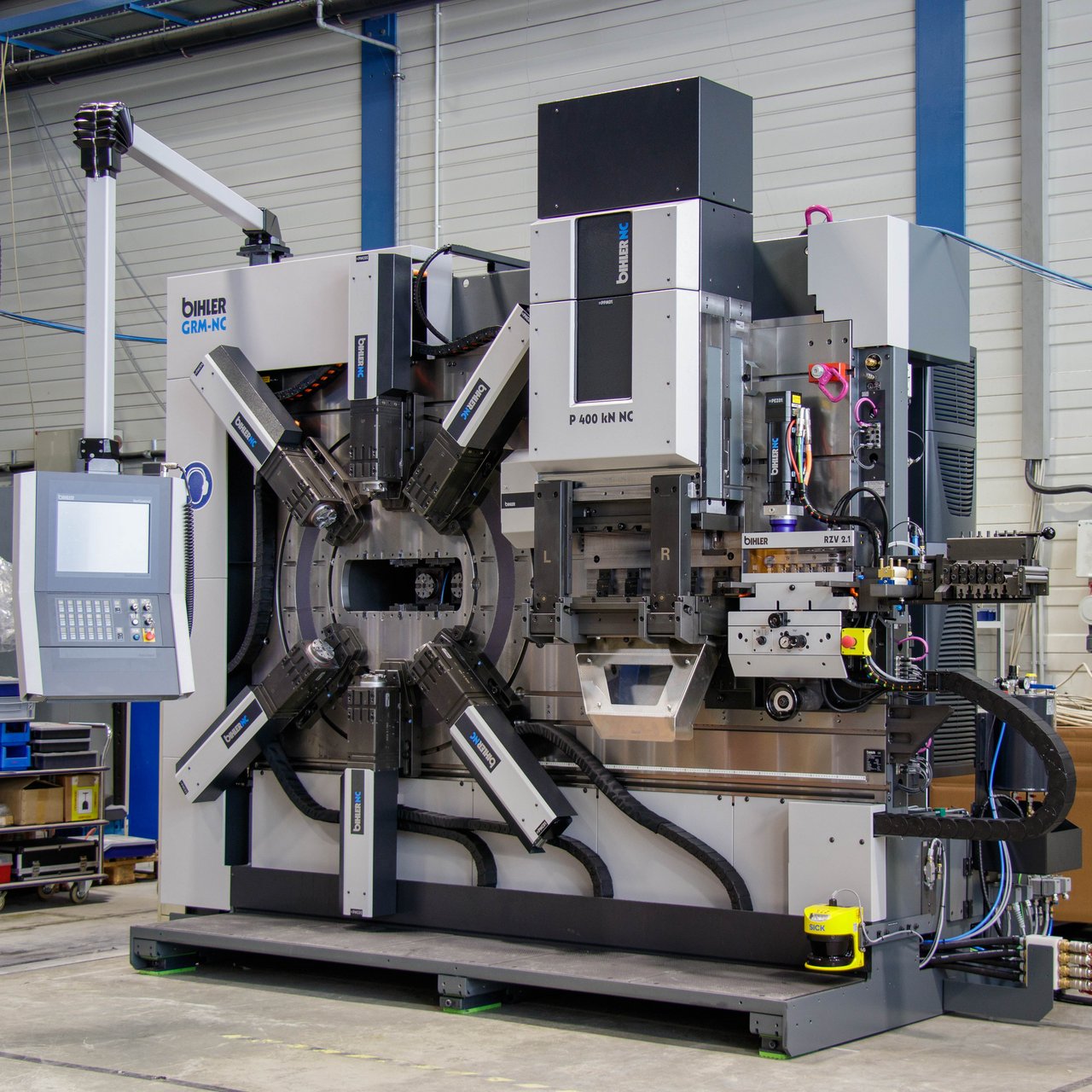
Manufacturer | J. Neu GmbH |
Model | 6-Axis Machine NSB090 |
Year of Production | 2019 |
Brief Description:
Freeform bending opens up completely new design options for bending round tubes and profiles. In the process, even high-strength materials can be bent for all radii with low cycle times using only one tube-specific toolset. The radii can be seamlessly connected and positioned in several planes. Freeform bending of different radii without tool change is made possible by the NISSIN principle, in which the tube is first pressed by a feed unit through a guide sleeve and then through a tube-specific bending die. The tube is bent in a spatial curve by translation and rotation of the bending die relative to the guide sleeve. The kinematics' dynamic control produces a transitionless three-dimensional tube geometry with changes in curvature and direction at every point. The bending area's material structure is preserved, which ensures high formability for subsequent processing, for example, by hydroforming. Another area of application for freeform bending is in areas where radii of different sizes characterize the workpieces. Also, large radii that cannot be bent on conventional bending machines can be transformed with high speed and accuracy in a single operation.
Technical Specification:
Bending Radius | 2D ... unlimited |
Bending Angle | 0° ... 360° |
Approximate Maximal Bendable Tube Length | 4500 mm |
Main Areas of Application:
- Freeform bending of round steel and aluminium tubes as well as profiles or any cross-section
Equipment:
- Two tools for bending round tubes (42.4 mm x 2.6 mm und 33.7 mm x 2.0 mm)
- A tool for bending square profiles
Photo Gallery:
Manufacturer | Baust Werkzeugtechnik GmbH (Langenfeld) |
Year of Production | 1999 |
Brief Description:
The rotary punching machine from Baust Werkzeugtechnik represents an economical alternative to conventional high-speed presses for the mass production of perforated and profiled sheet metal strips. The processing speed for thin sheet metal is up to 60 m/min. The sheet processor is used to unwind, roll-punch, and rewind the sheet metal strip. The sheet processor is adjusted to the speed of the de-coiler using a measuring wheel. Furthermore, this machine can be used for rotary clinching.
Technical Specification:
Drive Power of Re-/and Decoiler | 5.5 kW |
Drive Power Die Roll | 4.6 kW |
Sheet Throughput Speed | 0 ... 60 m/min |
Center Distance of the Tool Rolls | 286.48 mm |
Main Areas of Application:
- Rotary cutting/punching/piercing
- Rotary clinching
Equipment:
- Various tool rollers for rotary cutting
- Tool rolls for rotary clinching with elastomer hold-down clamp
- Tool rolls for rotary clinching with spring-based sheet hold-down clamp
- Machine control unit SIemens SPS S7
Photo Gallery:
Manufacturer | Blech-Tec GmbH |
Model | BT-500 |
Brief Description:
As the only combination bending machine, it unites swivel bending (folding), press brake bending and pressing on one machine. This offers a completely new flexibility. The unique design allows the different kinds of bending even in one program. The comfortable 2-finger guide supports these new possibilities additionally.
Technical Specifications & Equipment:
Bendingtye | swivel bending (folding), press brake bending and pressing |
Pressure | 6 t |
Accuracy | 0.01 mm / 0.1° |
Max. sheet thickness | 5 mm |
Max. bending width | 50 mm |
Tooling radii | 0.5 mm, 1 mm, 1.5 mm, 2 mm, 3 mm |
Main Areas of Application:
- Processing of spring steels
- Manufacturing of busbars