Research focus of reusable methods of diagnosis by analysis of aggregated data system for plant and machinery families
Description
The availability of systems is one of the highest goals of any plant operator. Increased availability means the current status of each sensor and actuator assess about the product to the entire system and before or in the case of failure to perform error compensation measures to maintain the system operation. At the same time the required product quality shall be achieved in all situations. This is far more than nowadays diagnostic systems and asset management systems (AMS) achieve and requires new and innovative methods, based on current and future trends in technology.
The Institute of Automation and Information Systems researches new and innovative methods for knowledge-based asset management systems, data-driven diagnostic methods in the context of Industry 4.0 and Cyber-Physical Production Systems (CPPS) in the complete plant lifecycle, and taking into account human factors when using human-machine interfaces.
Information gain by data aggregation from plant-wide data sources – A way from the data graves towards value creation
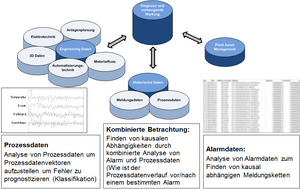
Each company has a flood of data from various interdisciplinary areas and different phases of the plant lifecycle, such as documents from the development phase of the system or data recorded (message and process data) during operation of the plant, for guarantee purposes. In both data sources are a lot of human know-how and information about interferences and troubleshooting. Both data sources often become data graves and the information about disturbances will not be extracted by analytical methods or not even aggregated for an information gain for an AMS.
A research objective of the chair in the area of knowledge-based asset management system is to research new methods of diagnosis in the field of data aggregation described above and this by new data-driven analysis techniques. In this process fault characteristics are analyzed from the data. Fault characteristics are not only characteristics that describe the malfunction, but also include the symptoms of a malfunction, the effect of a malfunction upon upstream and downstream processes and also upon troubleshooting, by observing the input of the plant operator in case of an error. The analyzed fault characteristics are transferred to the knowledge-based asset management system and used during the plant operation to automatically detect problems early and to perform compensation strategies in the sense of the Self-Healing Machine® to increase the operating time of the system.
The chair has already some of the above mentioned aspects implemented in various projects and shown what additional information for a knowledge-based asset management system are needed and how the system availability can be increased with these results - all with minimal overhead:
M2M communication of diagnosis methods and fault characteristics – a system warns the other
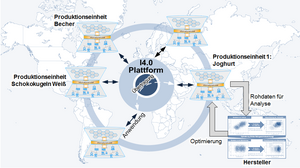
In terms of the value chain of a company, knowledge-based asset management systems and explore data-driven diagnostic methods should not only be used at one plant. By CPPS and Industry 4.0 future machines and plants worldwide will be interconnected and share diagnostic information. In the future, machines and plants will talk about the fault characteristics to transfer knowledge -based asset management information onto machines and plant families. Once obtained fault characteristics will be used system-wide and before a fault in an adjacent plant has occurred. Thus, a machine warns a machine of the same family of machines.
We as the Institute of Automation and Information Systems are one of the enabler and driver of CPPS and Industry 4.0. We are co-sponsors of the research network „myJoghurt“ for the demonstration of CPPS and Industry 4.0. Different plants in a university environment are interconnected and are operated in cooperation with each other. This research network demonstrates companies the opportunities and benefits in the context of networked autonomous communicating systems. The plants in the research network are cross-linked by artificial intelligences and can be reconfigured dynamically at runtime so that customer orders are processed on time – even in case of a failure. In case one plant fails completely, other plants take on that orders (also in the distributed system network), as long as the plants can realize the required functionalities for the production.
- I4.0 Demonstrator: MyJoghurt
- Multi-agent systems to increase machines' availability
- Research field: Distributed systems
In addition to that, Prof. Dr.-Ing. Birgit Vogel-Heuser is chairman of the VDI/VDE-GMA commitee 5.15. "Agentensysteme".Thus, we are in constant contact with companies and research institutions to jointly improve agent-oriented approaches in research and establish these in industry.
Visual support of plant operators in the context of Industry 4.0 – the human aspect should not be underestimated
There is a growing trend towards replacing the classic 2D plant monitoring and operation system by mobile devices and application-specific 3D visualizations. The performance of mobile display components is no longer an obstacle. Although the system networking and data aggregation, however, leads to an information retrieval, though it leads to the challenge to provide the plant operator with a suitable man-machine interface, to show the information gained from the various data sources. Here also the usability and acceptability of novel control elements has to be considered.
Our interdisciplinary and trans-disciplinary team – consisting of mechanical engineers, computer scientists, electrical engineers, mechatronics engineers and psychologists – provides application and research of new visualization capabilities. Backed by our engineering psychologists in industrial science we not only show the basic engineering-applicability of new visualization techniques and media, but demonstrate through empirical studies the benefit of new technologies for the end user and this with the inclusion of human factors with different technical training status. This expertise has already been demonstrated and proofed in several research projects:
- Augmented Reality for operator assistance and maintenance
- Interactive 3D visualization for operator assistance
- Research field: Human Factors
Research and Practice – Real industrial applications are the aim
Challenges are not only in exploring of new methods within the research foci of the chair and the application of these at (sterile) laboratory facilities, but also in the feasibility in the real and harsh industrial environment. We are supported by long-term and trusting cooperations of more than 30 reputable companies, both nationally and internationally – from manufacturing along process industry to hybrid processes.
Publications
- Folmer, Jens; Meyer, Heiko; Weißenberger, Benedikt; Vogel-Heuser, Birgit. Diagnosis of Automation Devices based on Enginering and Historical Data. In: IEEE International Conference on Emerging Technologies and Factory Automation (ETFA), 2012. doi: 10.1109/ETFA.2012.6489688
- Folmer, Jens; Li, Fang; ‚Wannagat, Andreas; Vogel-Heuser, Birgit. Engineering funktionaler Abhängigkeiten zur Steigerung der Verfügbarkeit von Produktionsanlagen. In: Entwurf komplexer Automatisierungsanlagen (EKA), Jumar , U. et al. (Hrsg.), 2010.
- Folmer, Jens; Vogel-Heuser, Birgit: Model-Based Approach to Generate Training Sequences for Discrete Event Anomaly Detection in Manufacturing. In: IFAC Conference in Embedded Systeme, Computational Intelligence and Telematics in Control (CESCIT), 2012. doi:10.3182/20120403-3-DE-3010.00080
- Folmer, Jens; Vogel-Heuser, Birgit: Computing Dependent Alarms for Alarm Flood Recuction. In: Transaction on System Signals and Design (TSSD), Vol. 8. No. 1, 2014.
- Vogel-Heuser, Birgit; Feiz-Marzoughi Bagher: Datenkopplung mittels UML-Modellen - Engineering- und IT-Systeme für Industrie 4.0 vernetzen. In: Atp edition Vol. 12, 2013, S. 26-37.
- Hufnagel, Johann, Frank, Timo, Vogel-Heuser, Birgit: Framwork for a Model-Based, Cross-Domain System Interconnection in Automation Technology. In 18th IEEE Conference on Emerging Technologies and Factory Automation (ETFA), 2013. doi:10.1109/ETFA.2013.6647981
- Pötter, Thorsten; Folmer, Jens; Vogel-Heuser, Birgit. Enabling Industrie 4.0 - Chancen und Nutzen für die Prozessindustrie. In: Bauernhansl, Thomas; ten Hompel, Michael; Vogel-Heuser, Birgit (Hrsg.), Industrie 4.0 in der Produktion, Automatisierung und Logistik, 2014, S. 159-171. doi:978-3-658-04682-8_17
- Vogel-Heuser, Birgit; Diedrich, Christian; Pantförder, Dorothea; Göhner, Peter: Coupling heterogeneous production system by a multi-agent based cyber-physical production system. In: IEEE International Conference on Industrial Informatics (INDIN), 2014. doi:10.1109/INDIN.2014.6945601
- Panförder, Dorothea; Mayer, Felix; Diedrich Christian; Weyrich, Michael; Vogel-Heuser, Birgit. Agentenbasierte dynamische Rekonfiguration von vernetzten Produktionsanlagen - Evolution statt Revolution. In: Bauernhansl, Thomas; ten Hompel, Michael; Vogel-Heuser, Birgit (Hrsg,), Industrie 4.0 oin der Produktion, Automatisierung und Logistik, 2014, S. 145-158. doi:978-3-658-04682-8_17
- Mayer, Felix; Pantförder, Dorothea: Unterstützung der Menschen in Cyber-Physical-Production Systeme. In: Bauernhansl, Thomas; ten Hompel, Michael; Vogel-Heuser, Birgit (Hrsg,), Industrie 4.0 oin der Produktion, Automatisierung und Logistik, 2014, S. 481-491. doi:978-3-658-04682-8_17
- Schweizer, K.; Vogel-Heuser, B.; Pantförder, D.; Gramß, D.: Förderlichkeit des Einsatzes von 3D-Pattern und Slider für die Fehlererkennung bei der Überwachung von Prozessdaten - ein Vergleich von jüngeren und älteren Operatoren (Novizen). In: Zeitschrift für Arbeitswissenschaft, Ergonomia Verlag, Stuttgart, 2013, S. 45-61.
- Pantförder, D.; Vogel-Heuser, B.: Benefit and evaluation of interactive 3D process data visualization in operator training of plant manufacturing industry. In: Proc. IEEE International Conference on Systems, Man and Cybernetics SMC 2009, San Antonio, 2009, 824—829. doi:10.1109/INDIN.2014.6945601
- Pantförder, D., Vogel-Heuser, B., Schweizer, K.: Benefit and evaluation of interactive 3D-process data visualization for the presentation of complex problems. In: Jacko, J.A. (Ed.): Human-Computer Interaction, Part II, HCII 2009. LNCS 5611, Springer-Verlag, Berlin Heidelberg, 2009. S. 869–878. doi:10.1007/978-3-642-02577-8_95