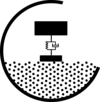
SOLID
Smart Soil Compaction Devices
Schlagworte
Digital Twin, Solution Space Engineering, Dynamical Systems Design, Multi-Body Simulation, Noise-Vibration Reduction, Human-Centered Design
Motivation
Digital twins for vibrating systems have significant potential to improve their performance. For instance, by utilizing a simulation model for the soil compaction process, including the vibratory rammer, performance can be enhanced while mitigating dynamic loads on the operator. This emphasizes leveraging digital twins for operator-focused vibrating system design, prioritizing well-being and operational efficiency.
Designing and operating within the digital twin framework allows for real-time monitoring of the procedure and, consequently, adjustments that ensure optimal performance. Moreover, advancing the system by integrating sensors allows for real-time data analysis and provides immediate feedback on crucial factors related to the process. This allows for enhancing the overall productivity and efficiency of the vibratory rammer.
Finally, the data-driven approach adds value not only to the design phase but also to the operational lifecycle of the vibrating system.
Zielstellung
This project aims to design a product that adheres to the multidisciplinary requirements of soil compaction, maneuverability, manufacturability, sustainability, and cost via solution spaces engineering procedures. The human operator's role within the system is essential to the requirements analysis and the design process. Ensuring compliance with safety and health standards concerning the operator's exposure to vibration and noise is crucial.
Finally, the project aims to virtualize the process via digital twin to exploit the framework's real-time performance tracking benefits and support maintenance and safety analysis. This approach ultimately leads to a more optimal and reliable product.
Ansatz
A proposed approach for addressing the design of the vibrating system involves utilizing the V-model. The V-model decomposes the quantities of interest for the system into design variables at the component level by establishing analytical or numerical relationships between them. Subsequently, using solution spaces, the design variables of components act as permissible intervals for the design variables related to the performance details of the system. In support of this concept, several essential engineering technologies are employed, including algorithms for solution box evaluation, multi-body simulations, finite element analysis (FEA), design of experiments, numerical optimization, surrogate modeling, and others.
Projektpartner
Wacker Neuson Group,
TUM - Zentrum Geotechnik
Finanzierung
Bayerische Forschungsstiftung
Projektdauer
September 2023 - September 2026