Self-X Material Flow Demonstrator
Testbed for research in the field of intralogistics and improvement of the interchangeability of modules
Brief description
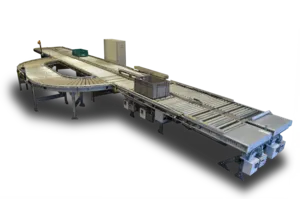
The chair of Automation and Information Systems owns the Self-X Material Flow demonstrator for implementing and evaluating different control concepts in the field of intralogistics. The conveyor hardware consists of two approx. 10.8 m long, driven roller tracks and an arc for in- and outfeed of transported material, which can be filled, emptied or manipulated in a different fashion. For the cross transport, there are corner transfer units at the end of both rows and in the transition zone of the arc. These corner transfer units are integrated into the main tracks and implemented as 3-track round belt conveyors.
The tracks are divided into separately controllable segments and can be actuated pneumatically or electrically, thus, allowing individual control of each roller conveyor. In addition, we have two stoppers to dam or delay the material flow. However, these can be made superfluous by an appropriate control strategy of the conveyor elements. On field level the demonstrator uses PROFINET communication, which is also used for connecting either a bar- or QR-code scanner. The information read by the scanner can be used for deciding whether the transported good is ejected towards the arc or not. For control purposes there are the following control systems available: CODESYS (Soft)PLC, Siemens S7-300, S7-1500 and Nanobox PC SIMATIC IPC227
Goals
Automated material flow systems are usually composed of pre-engineered and similar mechanical components, e.g. a certain type of roller conveyor, in order to reduce efforts in early development phases and to obtain a consistent hardware base. One application for the demonstrator is to reach the following research goal: We want to reflect the modularity of the hardware architecture, which is obtained by the usage of pre-engineered components, into the software to allow a component-wise composition and generation of the software (see research project aComA). The segment-wise actuation of the conveyor elements enables a “transported-good-oriented” programming, which means activating only those elements that carry material. In this case, segments can also be subsumed to so called “logistic modules” such as T- or U-units.
Additionally, we want to develop an approach for the automatic analysis and adaption of the interface and behavior of the modules to reduce the effort involved in developing backward compatibility for the modules. Therefore, due to the automatic analysis and adaption of the interface, the changeability of modules possessing a different version number is improved, which is also an essential challenge to realize the current trend of automation and data exchange in manufacturing technologies. The subsequent code synthesis will then apply the changes to the interface according to the neighboring elements. In order to reduce the engineering effort, the analysis of changes as well as the adjustment of the interface after synthesizing the code shall be automated (see research project aComA). By using the demonstrator as a test bench for the above research goals, the chair of Automation and Information Systems helps to enhance efficiency in the development of intralogistic automation systems in industrial practice and is able to verify the applicability of the developed approach on a real industrial demonstrator.